Injection Molding Business: A Complete Guideline of How to Start
2024-03-27 16:57:49
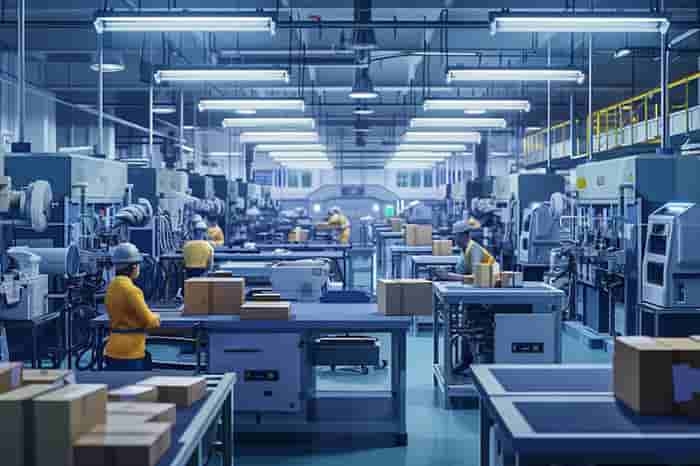
In the thriving plastic injection molding market, the demand for high-quality injection-molded products is on a constant rise. The revenue of the injection molding business market has been steadily climbing, reaching a staggering USD 285.5 billion in 2024. It is projected to soar to USD 431.6 billion by 2033, at a CAGR of 5.1% during the forecast period 2024 – 2033. This highly profitable market is brimming with opportunities, making it an ideal venture for those with a keen interest in the injection molding business.
The market for injection-molded products spans a wide spectrum of industries, including medical, automotive, consumer electronics, pharmaceuticals, telecommunications, food and beverage, construction, and packaging. These industries heavily rely on injection molding businesses to manufacture plastic products, due to their robustness, long-lasting features, and ability to withstand pressure, temperature, and impact.
Starting an injection molding business requires careful planning and investment. Here are the key components:
- Factory Space: Securing a sizable factory space is paramount to kickstart your injection molding business. This space should accommodate the injection molding machines, provide ample room for workers, and allow for easy movement within the facility.
- Operational Licenses: Obtaining the necessary licenses and permits from local relevant authorities to legally operate your business.
- Skilled Labor and Expertise: The backbone of your injection molding business, hiring experienced technicians and operators who understand the injection molding process is crucial. A skilled workforce is not just an asset, but a necessity for the smooth operation of your molding plant. Whether automated or manual, your workers should be trained and experienced in managing the machinery and production processes, ensuring the highest quality of your products.
- Raw Materials: Plastic injection molding requires a steady supply of raw materials, such as plastic resins, additives, and colorants. Establishing reliable supplier relationships is key to ensuring uninterrupted production and efficient operation.
- Machinery and Equipment: Invest in reliable injection molding machines, molds, temperature control systems, robotics, and inspection equipment.
Further reading: What are Fundamentals of Injection Molding? 3 Keys to Plastic Injection Plant
What Machinery and Equipment Required?
- Injection Molding Machine: Injection molding machines come in various sizes, specifications, and models, depending on the material and size of the plastic products you intend to manufacture. Choose durable and high-quality injection machines that are compatible with the type of products you plan to produce. Avoid cheaper machines that may compromise the quality of your products.
- Injection Mold: Custom molds are essential for creating specific product shapes and designs. There are two main types of injection molds: cold runner and hot runner molds. When choosing a mold type for your injection molding business, consider factors such as production volume, part complexity, material cost, and desired cycle times.
- Mold Temperature Controller (MTC): To ensure product quality and reduce cycle times, mold temperature controllers can help achieve uniformity in the molded parts, reduce defects, and improve the overall quality of the products. It is NOT essential equipment, but it can reduce cycle times by ensuring that the molten material solidifies at a consistent rate, allowing for faster production.
- Robotics/Automatic Handling: Integrating robotics into an injection molding business for automated part handling can improve efficiency and labor-cost savings. However, it is NOT essential equipment.
- Inspection Equipment: Ensure quality control with equipment for measuring dimensions, testing strength, and detecting defects for the injection-molded products.
- Auxiliary And Equipment: Other Equipment: For smooth operation, include equipment for cooling towers, hopper dryers, chillers, granulators, recycling equipment, and so on.
Further reading: Choosing the Right Injection Molding Machine: A Comprehensive Guide
Injection molding offers several key advantages:
- Production Efficiency: Machines can produce thousands of moldings per hour, and electric machines make the process energy-efficient.
- Design Flexibility: Manufacturers can choose the type of thermoplastic and mold design for each part, allowing for large-scale production.
- Production Consistency: The process can provide thousands of components quickly and consistently with proper parameters.
- Cost-Effective For Large Volume Production: Once a molding machine is built, it can provide several molded components, reducing the cost per component.
- Consistent Product Quality: When set up correctly, the process can produce high-quality, detailed components consistently.
- Material Durability: Components made with high-quality thermoplastics are durable and consistent in quality.
Types of Plastics Used
Plastics used in plastic injection molding include:
- High-density polyethylene (HDPE) and Low-density polyethylene (LDPE): These provide good tensile strength, moisture resistance, and recyclability.
- Acrylonitrile Butadiene Styrene (ABS): Tough and impact-resistant, widely used for acid-resistant components.
- Polycarbonate (PC): Low shrinking rate, good dimensional stability, transparency, and heat resistance.
- Aliphatic Polyamides (PPA): Offer good hardness, stiffness, and impact strength.
- Polyoxymethylene (POM): High hardness, stiffness, strength, and toughness, with good resistance to hydrocarbons and organic solvents.
- Polymethyl Methacrylate (PMMA): Provides optical properties, high gloss, and scratch resistance.
- Polypropylene (PP): Offers resistance, flexibility, high elongation, and resistance to acids and bases.
- Polybutylene Terephthalate (PBT): Good electrical properties, ideal for power components and automotive applications.
- Polyether Ether Ketone (PEEK): High-temperature, high-performance resin with heat resistance, flame retardancy, strength, dimensional stability, and chemical resistance.
Further reading: Understanding the 10 Most Common Injection Molding Materials
Despite its advantages, injection molding also presents challenges such as:
- Initial investment costs
- Technical complexity
- Quality control issues
- Environmental concerns related to plastic waste
Many businesses have found success in the injection molding industry by focusing on innovation, quality, and customer satisfaction. These success stories inspire aspiring entrepreneurs.
- Dental Flossers and Interdental Brushes: How to Manufacture High-Quality Dental Flossers and Interdental Brushes
- PET/RPET Tableware: Replacing Melamine and Acrylic: The Rise of PET/RPET Tableware in Affordable Markets
- Electrical Instruments: The Role of Injection Machines in Electrical Instruments Equipment Production: A Success Story
- Flower Pot: Unlocking the Potential of Injection Molding Machines - Plastic Flower Pot Production
- Automotive Parts: Injection Molding Machine: Key to Precision Manufacturing of Automotive Parts
- Bottle Caps: The Science Behind Plastic Caps: How are Plastic Bottle Caps Made
- Pallet: The Process of Key Role for Warehousing: Plastic Pallet Injection Molding
- Dual Color Hair Clip: Dual Color Hair Clip Machine - How To Make Your Own Dual Color Hair Clips
- Headphone Outer Cases: How the Production of Headphone Outer Cases Works? - Dual Injection Molding Machine
What Future Trends in Injection Molding Business?
The injection molding industry is evolving with advancements in technology, materials, and processes. Trends such as additive manufacturing, automation, and sustainability are shaping the future of injection molding.
Further reading: Sustainable Injection Molding Manufacturing: Two-Platen Injection Machine for Global Markets
When sourcing plastic injection molding services, consider factors like experience, capabilities, quality standards, and cost-effectiveness. Selecting the right injection molding machine supplier is paramount for your business's success. When evaluating potential suppliers, consider factors such as machine reliability, performance capabilities, technical support, and after-sales service. It's essential to choose a supplier that offers a diverse range of machinery options to accommodate varying production needs and budget constraints. Additionally, prioritize suppliers who provide comprehensive training programs and ongoing assistance to ensure optimal machine operation and maintenance.
Your Injection Molding Partner - Huarong Group
With a reputation for reliability, performance, and excellent customized service, Huarong offers a comprehensive range of injection molding machine options suitable for various production requirements, including horizontal injection machines, vertical injection machines, and automation turn-key solutions. Our commitment to providing top-notch machines and after-sales service ensures your business operates smoothly and efficiently. Please feel free to contact Huarong and trust us as your molding partner.
- Group Name: Huarong Group
- Brand: Huarong, Yuhdak, Nanrong
- Service Offerings: Injection Molding Machine, Vertical Injection Molding Machine, Injection Molding Automation
- Tel: +886-6-7956777 #521
- Address: No.21-6, Zhongzhou, Chin An Vil., Xigang Dist., Tainan City 72351, Taiwan
- Official Website: https://www.huarong.com.tw/
Previous news: Two Platen and Three Platen Injection Molding Machine Difference
Next news: 10 Common Plastic Injection Molding Material and Characteristics