How the Production of Headphone Outer Cases Works? - Dual Injection Molding Machine
2023-02-20 13:51:56
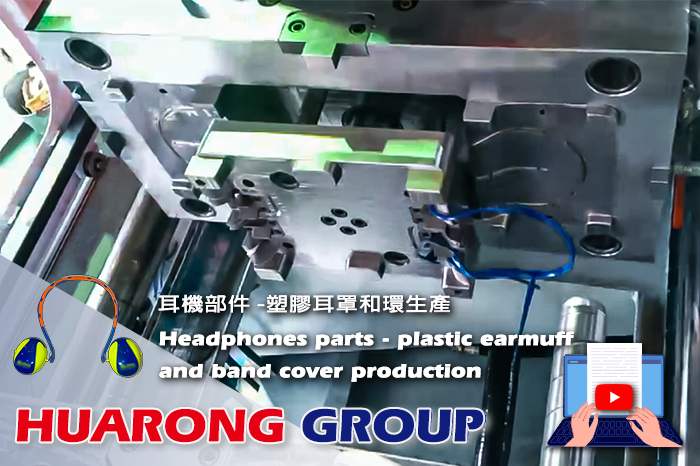
Headphone parts - metal and plastic parts
Headphones are used frequently. On the way to commute and during exercise, wear headphones in a noisy environment to enjoy the sound you want to hear and immerse yourself in music. Depending on the environment and usage, the survey shows that the average number of headphones owned by a person is about more than 4 pairs.
Headphone form factors can be divided into four categories: circumaural (over-ear), supra-aural (on-ear), earbud, and in-ear for a person to choose the right pair. The behind-the-scenes engineering of earphone production is important. Manufacturing a set of earphones is divided into metal parts and plastic parts. For metal parts, the material processing, cutting, and wire assembly are all steps that rely on CNC processing, The test machine checks the quality. For plastic parts, it starts with selecting the plastic material, different plastic materials have various properties such as lightweight, acid and alkali resistance, high strength, high plasticity, good toughness, and high-temperature resistance according to the product's positioning in the market. Using injection machines and injection molds produces the shape and design of the earphones.
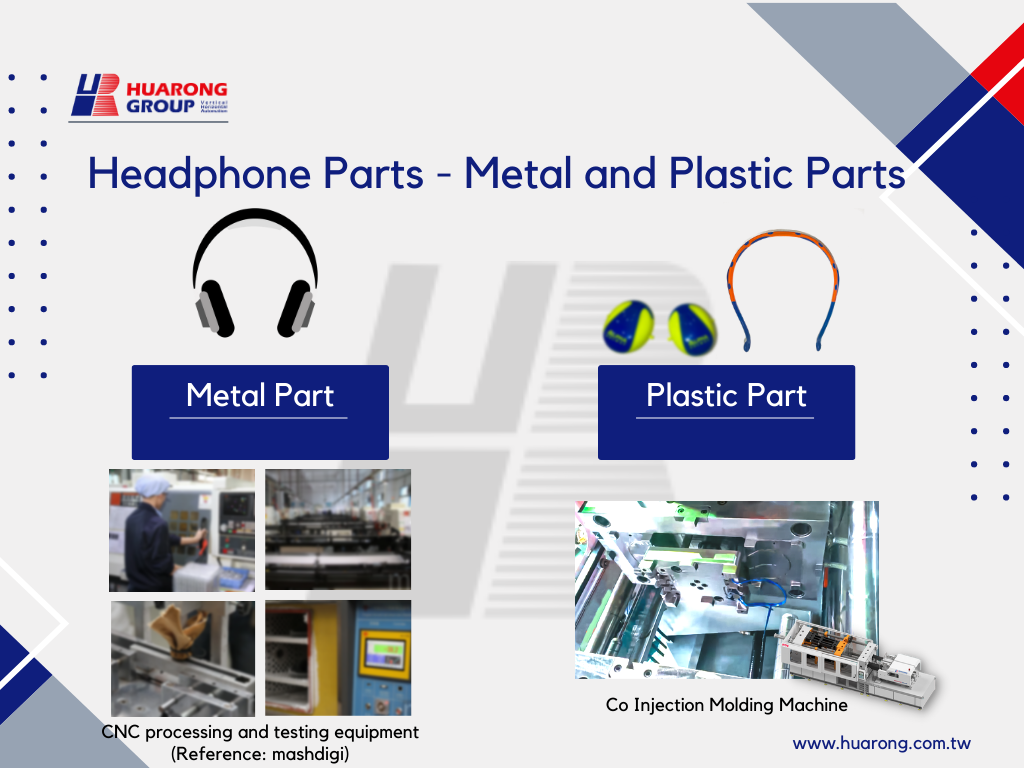
Headphones parts - plastic earmuff and band cover production
Huarong is an experienced injection molding machine manufacturer and provides customers with durable injection machines to meet customers’ production needs from injection machines, injection molds, and automation to intelligent systems to meet customers' needs for injection molding.
Using two-shot injection molding to inject two different colors/materials into a single object can improve production efficiency, make the appearance of the product more aesthetically pleasing, and maintain consistent product quality. This machine is widely used, including audio equipment, home appliances, daily necessities, and automotive parts.
About Huarong’s injection molding machine
Machine | HDC Series (Dual injection)
Advantages |
- Save time and money:
Dual injection machines are capable of simultaneous injection molding of two different materials. It saves production time and costs by enabling multiple products in one operation - Improve product quality and increase production flexibility:
The dual injection machine can inject two different plastic materials in the same mold to be multi-color and multi-layer injection products during the injection process. Thereby, it increases production flexibility and improves the appearance quality of the product. The strength and durability of machines enable enterprises to respond more quickly to market changes and customer needs. - Reduce production losses:
During the operation of the dual injection machine, the product can be produced simultaneously, avoiding the need to replace the mold for the package injection, resulting in machine readjustment, thereby reducing production loss and scrap rate and improving production efficiency and economic benefits. - Save plant space:
The dual injection machine has two injection units in one injection machine, which saves plant space and reduces the production cost and site costs.
Feature |
- Patented design for rotary table
Dedicated designs for accurate positioning and lean-free. - Patented Groove design with the tie-bars
Balanced & equalized clamping spread. - Optional
- Servomotor-drive rotation
- T-type / L-type injection (tri-injection)
- Rotary table and shaft sharing system

Plastic headphone earmuff and band cover production
▶️Video highlights
Machine model | HDC Series
Plastic product | headphone band & headphone earmuff
Row material | PP+TPE
Mold cavity | 1
YouTube:
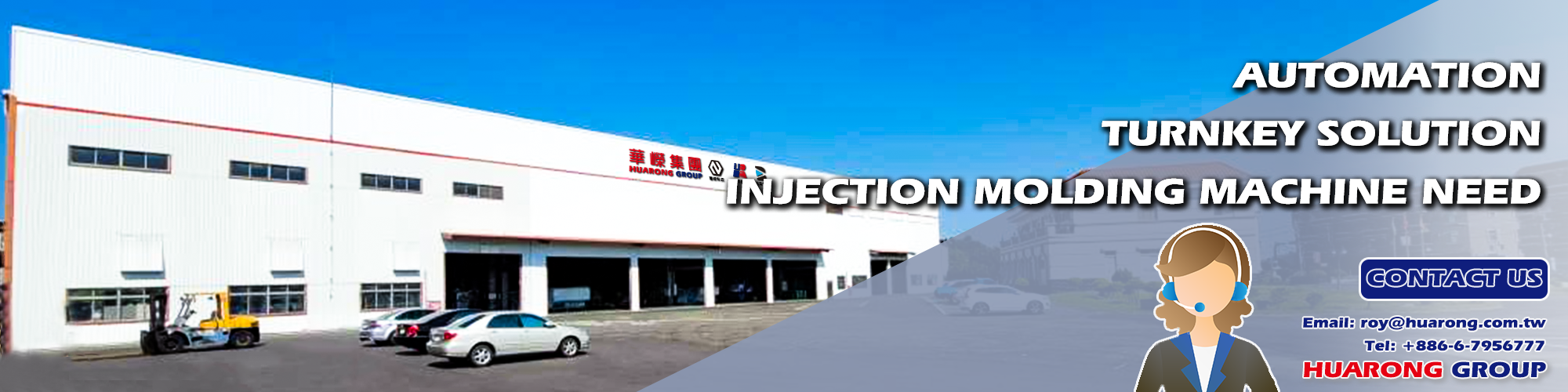
Previous news: Two-Platen Injection Molding Machine Obtained Patent Certification to Provide Better Machine
Next news:What is Dual Injection Molding?