Choosing the Right Injection Molding Machine: A Comprehensive Guide
2022-08-11 17:25:36
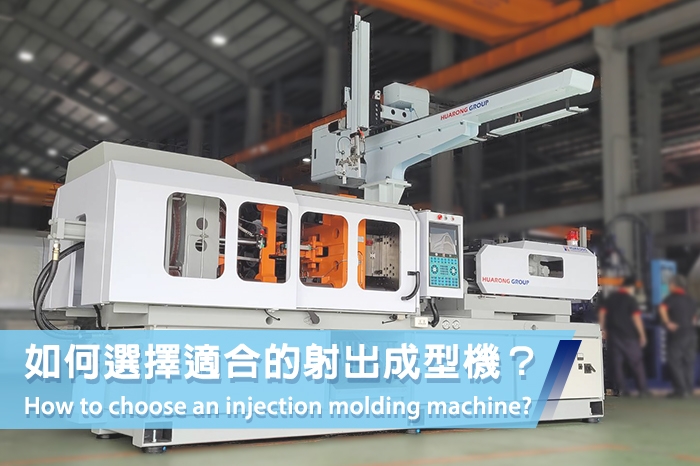
In the realm of injection molding factories, three key elements stand out: "equipment," "mold," and "management." Among these, "equipment" specifically refers to the injection molding machine, a pivotal component that should add value to your production. A suitable injection molding machine ensures stable production, easy operation, and convenient maintenance, ultimately meeting your production needs and creating value for your customers.
Injection molding machines come in two primary types based on clamping: horizontal and vertical. At Huarong, we continually enhance our product line of both horizontal and vertical injection machines to cater to varying plastic and production requirements. This ensures that our machines meet the diverse needs of customers producing different plastic products.
To select the most suitable injection molding machine, consider two main aspects: the machine itself and the plastic product.
Injection Molding Machine Components
- Clamping Unit: Focuses on the size of the mechanism, ensuring that the mold fits the machine and allows for automatic ejection of the product.
- Injection Unit: Evaluates the plasticizing ability, ensuring sufficient injection volume and plasticizing capacity.
- Power Unit: Considers the power system to ensure it meets the machine's requirements.
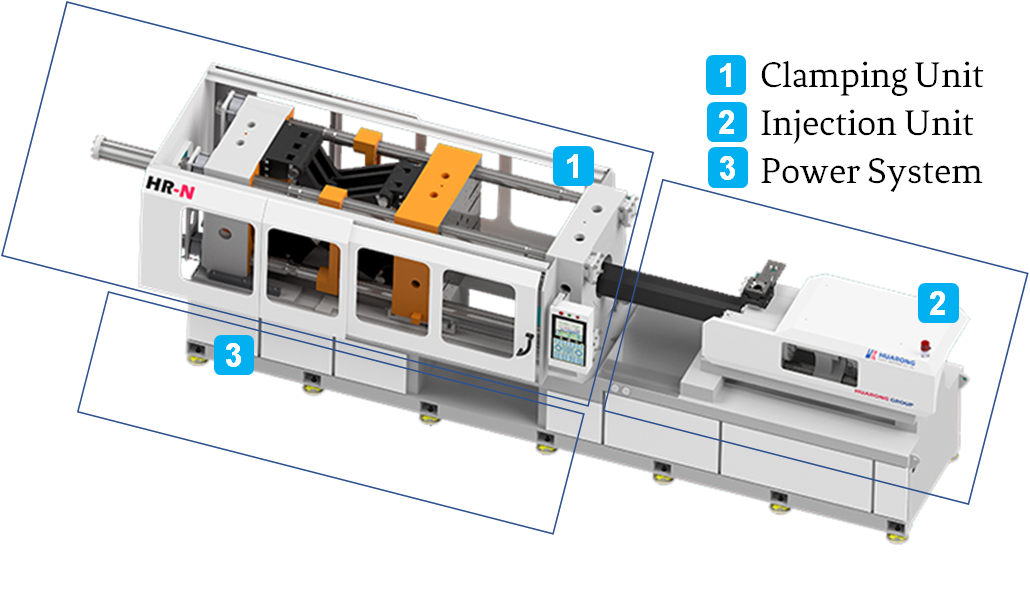
Clamping Unit: Size of the Mechanism
The clamping unit's size is determined by factors such as tie bar distance, opening stroke, and mold thickness. These factors directly impact mold installation, automatic ejection space, and mold clamping capability.
Tie Bar Distance
The length between the four tie bars affects the mold installation space and whether the space can accommodate the size of the mold.
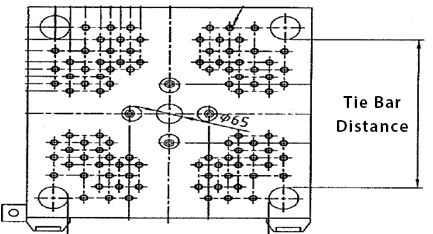
Mold Opening Stroke
The mold opening stroke refers to the displacement distance from which the movable platen is bent and straightened to the greatest extent by the toggle. This distance affects whether there is enough space for the plastic product to fall automatically after being ejected.
Regarding the mold opening stroke, it is better to have it greater than the sum of the sprue length and twice the height of the plastic product.
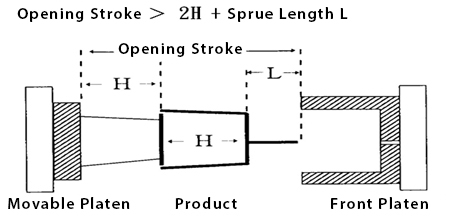
Mold Thickness
The mold thickness range refers to the difference between the thickest and thinnest molds that can be clamped. When selecting, please refer to: Maximum mold thickness (upper limit of mold) ≧ Mold thickness ≧ Minimum mold thickness (lower limit of mold).
Injection Unit: Plasticizing Ability
Consider the shot weight, injection pressure, and injection rate of the machine. These factors ensure adequate plasticization and injection volume.
Shot Weight
The shot weight of an injection molding machine is calculated by multiplying the injection volume by the plastic melt density (g = vρ). Typically, the shot weight listed on the machine's specification sheet is based on PS material. However, when evaluating the shot weight for other materials, it's important to consider unit conversions and safety factors. To ensure the injection unit meets production requirements, it's recommended to provide the manufacturer with information such as the type of plastic, product weight, and number of mold cavities.
Injection Pressure
The injection pressure needs to be considered based on the characteristics of the plastic, such as its fluidity, shrinkage rate, and product properties. The setting of injection pressure should generally be high, not low. A higher injection pressure is helpful for the injection molding of engineering plastics.
Injection Rate
The injection rate refers to the maximum volume of molten plastic injected from the nozzle in a unit of time and also represents the speed of the molten plastic passing through the nozzle. In theory, the product with thinner thickness has a faster injection rate, because the plastic will rapidly cool in the mold and lose its fluidity, resulting in insufficient plastic filling.
Power System
The size of the power system depends on the relational formula between the injection pressure and the injection rate. Sometimes, customers have production requirements for a "high injection rate" or "fast production cycle time." In such cases, the motor and pump can be increased to achieve the desired effect under constant system pressure.
To avoid unnecessary energy loss, consider opting for a servo hybrid power control system. This system enables precise control of pressure and flow in each process, ensuring that the system outputs only as much energy as needed. This approach eliminates excess energy consumption, resulting in significant energy savings.
Advantages of Servo Hybrid System
The servo hybrid power control system offers several advantages, making it a preferred choice for many injection molding applications:
- High Precision and Stability: The system provides high precision, fast response, and excellent stability, ensuring consistent and reliable performance.
- Energy Efficiency: It offers a high energy-saving ratio, reducing overall energy consumption and operational costs. The system only outputs as much energy as required, minimizing wastage.
- Low Noise and Cooling Requirements: The servo hybrid system operates quietly, creating a more comfortable working environment. Additionally, it requires less cooling water, further enhancing its energy efficiency.
- Long Service Life: The system has a long service life and low maintenance costs, providing durability and reliability over extended periods of operation.
- Wide Applicability: It is suitable for a wide range of plastic products, offering versatility and adaptability to various production needs.
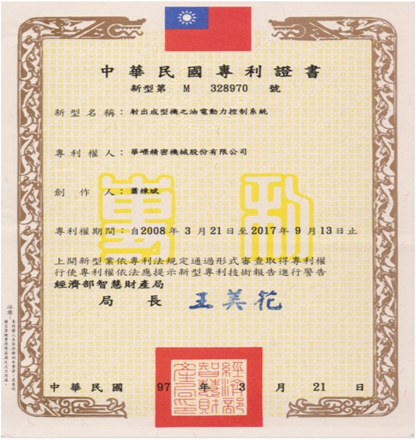
Currently, the variety of plastic products on the market is increasing. However, standard injection molding machines may not meet the requirements due to factors such as raw material usage and product design. It's crucial to assist customers in choosing a suitable injection molding machine.
Conditions
Various types of injection machines are available, and the choice of model depends on the product molding conditions. It's essential to first understand the products and their intended uses.
For instance, High-Speed Injection Molding Machines are suitable for thin-walled products. This is because the plastic cools rapidly in the mold, losing its fluidity and potentially leading to insufficient filling. Dual Injection Molding Machines are ideal for products with dual-color or dual-material injection requirements, such as automotive lighting.
Further ready: Break the stereotype of dual injection design and break through possibility of dual-shot production
For products made of PVC or PET, specific adjustments to the injection molding machine configuration are necessary. Both PVC and PET injections require special screws, and PVC Rigid Injection Molding Machines are designed with width-extended shields. PET Preform Injection Molding Machines need to be equipped with a dehumidifying dryer and mold dehumidifier to keep the plastic dry.
Huarong is one of Taiwan's leading injection molding machine manufacturers, offering a wide range of models. We can customize machines to meet your specific injection molding needs and ensure we fulfill all your requirements.
Size and Weight
When the size and weight of a product are larger, the tonnage of the machine must increase accordingly. As the size of the mold accommodating the product increases, the clamping force must also increase to avoid product flash. Providing product drawings or samples can help the injection molding machine manufacturer assist you in choosing a suitable machine.
For long and large products like chairs or barrels, consider a Two-platen injection molding machine with a longer opening stroke.
Plastics
If your product requires high-temperature resistance, consider using BMC (Bulk Molding Compound) as the plastic material. BMC is commonly used in industries such as electric motors, electronics, transportation, and construction.
When using BMC, it's important to choose a Bulk Molding Compound Injection Molding Machine. Unlike standard injection molding machines, this model heats the material to solidify the product. It requires a special anti-corrosion, wear-proof screw and is suitable for producing anti-corrosion, high-temperature resistant, and insulation products.
▶️YouTube:
Choosing the right injection molding machine involves meticulous consideration of various factors to avoid waste and maximize efficiency. At Huarong, we are committed to providing comprehensive advice and consultation, ensuring you find the perfect fit for your industrial needs. Trust us to be your reliable partner in the realm of injection molding machinery. We offer a broad range of models to cater to your specific requirements. Our core value of "Quality-Innovation & Industry-Alliance" drives us to continually improve and innovate, helping you build a smart, efficient factory. Please feel free to contact Huarong.
- Group Name: Huarong Group
- Brand: Huarong, Yuhdak, Nanrong
- Service Offerings: Injection Molding Machine, Vertical Injection Molding Machine, Injection Molding Automation
- Tel: +886-6-7956777 #521
- Address: No.21-6, Zhongzhou, Chin An Vil., Xigang Dist., Tainan City 72351, Taiwan
- Official Website: https://www.huarong.com.tw/
Previous news : Installation of injection molding machine, what should be paid attention to?
Next news : What is injection molding machine? By clamping mechanism to choose injection molding machine model