Injection Molding Machine Maintenance PDF and Checklist
2024-05-17 11:55:48
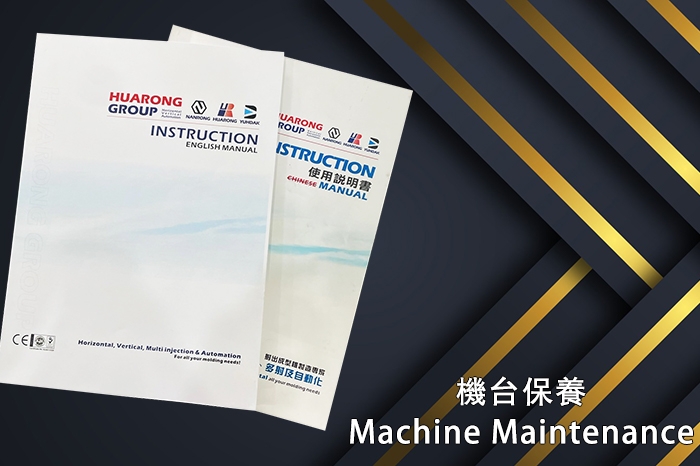
Welcome to the injection molding machine maintenance guide. In this article, we will discuss the crucial aspects of machine maintenance to ensure its optimal performance and longevity. Whether you are a seasoned professional or just starting out with injection molding, this guide will provide valuable insights and practical tips in three parts. Let's dive in!
Injection molding machines are complex pieces of equipment that require regular maintenance to operate efficiently. After machine installation and operation, diligent maintenance can not only prolong the machine's life but also play a crucial role in ensuring consistent product quality. Neglecting maintenance can lead to costly repairs, downtime, and subpar product outcomes.
The hydraulic transmission of an injection machine uses hydraulic oil as the working medium to transmit energy, pressure, or power. The quality of hydraulic oil and seals directly affects the system's stability and product quality. Here are some key maintenance tips:
1. Selection of Hydraulic Oil
Use the hydraulic oil model recommended by the manufacturer or a higher-specification alternative. Ensure the oil has good viscosity, cleanliness, oxidation resistance, wear resistance, foam resistance, corrosion resistance, and lubricity. Here are some selections provided for different usages for reference:
- For machine:
- For carriage: Endured temperature and extruding, drop point 170~200℃
- For grease oil: It needs infusion once each month
- For slide-way oil of lubrication system:
2. Regular Oil Testing
Perform regular tests to detect changes in oil properties and decide whether to change the oil. Use visual methods such as appearance tests, drop tests, and finger rubbing to assess the oil's condition.
3. Maintain Proper Oil Temperature
The suitable temperature range is 40-50°C as the machine is operating. Monitor the temperature closely to avoid issues such as seal hardening and reduced processing energy consumption.
4. Regular Oil Changes
Change the hydraulic oil every 5000 hours of operation or at least once a year to prevent the accumulation of sludge and dirt that can lead to system failure.
5. Clean the Inside of the Oil Tank
After the machine runs for 3 years, some impurities will remain inside the oil tank. Drain the old oil and clean the tank with flour and water to remove oil stains and impurities. Huarong designed the oil tank to be detachable, and you can follow Huarong’s instructions on page 64 or contact Huarong to get it.
6. Clean the Air Filter
Regularly clean the air filter to prevent dirt from entering the oil tank and affecting oil quality.
7. Clean the Oil Filter
Regularly clean or replace the hydraulic oil filter to prevent clogging.
8. Clean the Inside of the Cooler
Regular cleaning of air coolers is essential to maintain their efficiency and prevent issues like internal blockage or fouling. It is recommended to select soft (no minerals) as the cooling water and clean the cooler at least once a year or more frequently if its performance has decreased.
Tip:
- Remove the cooler cover, use nylon preparation or clean preparation to wash the dirt inside the cooler, or use 0.6~0.8% hydrochloric acid to wash the circulated inside the cooler under the oil cooler assembled well.
- Remove the two extremity covers and use an air gun to clean the circulated water inside the copper pipe.
- Lock the two extremity covers and oil seal to the original condition, and connect the cooling water.
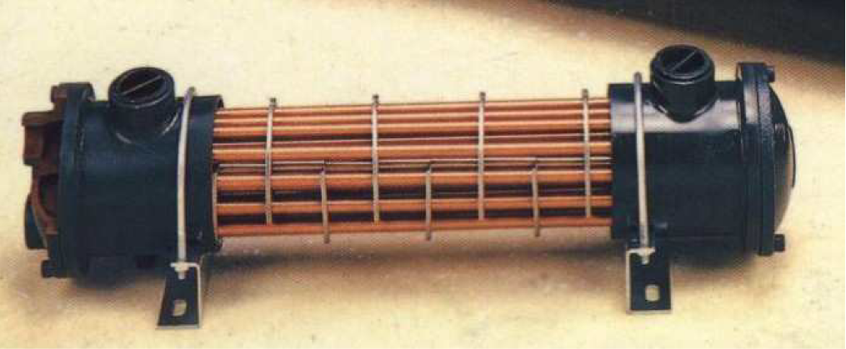
9. Clean the Oil Valve
Remove and clean the oil valve to prevent dirt buildup that can affect the valve's performance.
10. Replace the Bypass Filter Element
Regularly replace the bypass filter element to keep the oil suction pipe unobstructed.
11. Oil Pipe Joint Inspection
Inspect the oil pipe joints for signs of looseness and tighten them as necessary. To prevent oil leaks, replace any pipes showing signs of aging.
The electrical system of an injection machine requires regular inspection and maintenance to ensure its proper functioning. Here are some key maintenance tips:

1. Turn Off the Power for Safety
Always turn off the power before performing any maintenance tasks.
2. Wire Connector Inspection
Check the wire connectors regularly for tightness and damage. Loose or damaged connectors can affect signal transmission.
3. Motor
Clean the motor annually to avoid dust buildup that can cause heating problems and ensure proper overload protection.
4. Heating Tube and Thermocouple
Check and tighten the heating tubes regularly to ensure effective heat transfer.
5. Electromagnetic Contactor (AC/DC Electrical Box Maintenance)
Check the electromagnetic contactors regularly for proper functioning, and if they are overheating or damaged, replace them if necessary.
6. Computer Control Part
Inspect computer control parts for any malfunctioning components. Ensure the working power supply voltage, temperature, and humidity are within acceptable ranges.
The mechanical system of an injection molding machine plays a critical role in its performance and longevity. Here are some key maintenance tips:
1. Platen Parallelism
A parallel of the movable platen and fixing platen directly influences the precision of the machine. Ensure the machine platens are parallel to avoid uneven mold closing. Regularly adjust the platen parallelism to prevent product failure and equipment wear.
2. Mold Thickness Adjustment
Check and adjust the mold thickness regularly to ensure smooth, long-term production.
3. Timing and Quantitative Lubrication Control Inspection
Keep all mechanical moving parts of the lubrication system properly lubricated to prevent wear.
4. Machine Operation Inspection
Regularly inspect machine operations for any abnormalities to reduce and prevent vibration to avoid accelerated wear.
5. Bearing Inspection
Regularly check bearings for abnormal sounds or temperature rises and replace them if necessary.
6. Injection Unit Maintenance
The injection unit is composed of a hydraulic motor, dual twin-hydraulic cylinder, barrel, and screw and heater component, etc. The injection unit is the core system of the full machine. The power of the hydraulic motor pushes the barrel and screw to rotate and pass the plastification function of the heater component to gain a full operation process of the injection system. So, it must be noticed the maintenance of the injection unit.
Tip:
- When cleaning the material funnel, the injection molding material must be cleaned clear.
- Use the processing plastics two times; best to confirm that they do not have metal impurities, if mix the metal impurities will damage the screw, barrel, and screw tip; put a powerful magnet in the entrance under the bottom of the material funnel to prevent the obsession from metal impurities.
- Before the screw and barrel enter plastics at the charging material, please limit the speed to 40rpm and charge the material slowly. After the supplies are melted, they flow out via nuzzle and then bring the speed up to the normal rotational speed, preventing the check ring from causing friction and block phenomenon during fast rotating in no material state.
- Please use PP and PE plastics for purged work for PVC, POM, and easy-to-resolve plastics.
- Remove nuzzle and screw tip; avoid heating above 400℃, or it will reduce the strength of the component and cause broken.
- When installing the barrel, the locking moment of the screw should be proper; it will cause the internal diameter of the barrel to be out of shape to lock the application of force too big, causing such bad phenomena as the check ring will be damaged.
- It must daub the heat-resisting lotion in the 2 ~ 3 tooth positions of the whorl tooth end; if it does not daub the heat-resisting lotion, the whorl position will be oxidized and will be difficult to remove thereafter.
- Every fixed screw must be checked regularly.
- Allow cooling water and the material entrance to flow freely, preventing the injection cylinder from overheating and causing the oil seal to wear out.
- Prevent stepping on the barrel cover or hydraulic pipes.
- Must be heated 20 –30 minutes before material charging.
- If plastics stick together on the heater bands, they should be cleaned up immediately.
Daily Inspection Checklist
- Electrical System
- Do not power on unnecessarily: Avoid powering on the machine when checking high-voltage parts.
- Prevent water ingress: Ensure cooling water doesn't flow into the control cabinet during mold changes.
- Monitor temperature: Check the control cabinet temperature to prevent electron plate damage.
- Replace old relays: Replace old relays with new ones specified by the manufacturer.
- Hydraulic System
- Maintain pressure temperature: Keep pressure oil temperature between 30°C and 50°C to prevent oil oxidation.
- Monitor oil viscosity: Check oil viscosity to prevent pump damage and leakage.
- Check for water leakage: Inspect the oil cooler regularly to prevent water from entering the oil cylinder.
- Replace pressure oil: Replace pressure oil and clean the oil screen every 3,000 to 4,000 hours of machine operation.
- Address oil valve issues: Clean the oil valve core with diesel oil or kerosene to remove foreign bodies.
- Clamping Unit
- Lubricate hinge: Properly lubricate hinge parts to ensure a long service life.
- Keep tie bars clean: Maintain the cleanliness of tie bars and lubricate sliding feet and rails.
- Operate at appropriate pressure: Avoid clamping molds under insufficient or excessive pressure.
- Injection Unit
- Lubricate guide bar: Keep the guide bar lubricated and the injection platform surface clean and dry.
- Use appropriate materials: Only use plastics, pigments, and additives in the hopper.
- Monitor melting pot temperature: Do not power on the melting motor until the melting pot reaches the preset temperature.
- Regularly check parts: Inspect all parts regularly and tighten any loose parts.
Regular Weekly Inspection Checklist
- Check the heater to see if it is disconnected or poorly connected (according to the perimeter indicator).
- Check if any oil leakage occurs. Even if the leakage is small, it needs to be solved.
- Check for an auto lubricator. Check frequently as lubricating is 30 minutes per each. (Lub. oil for all toggles' moving parts, moving platen, and cross platen)
- Check the machines' screws and nuts that if any screws or nuts are loosening.
- Check the nozzle's heater band to see if any resin is attached to the end of the wiring and the nozzle's heater band.
- Clean the remaining useless hydraulic oil inside the machine.
- Clean the whole body of the machine. Clean the materials of greasy dirt, fur, waste oil, dust, and unnecessary attachments. After cleaning, it is better to apply anti-rust paints.
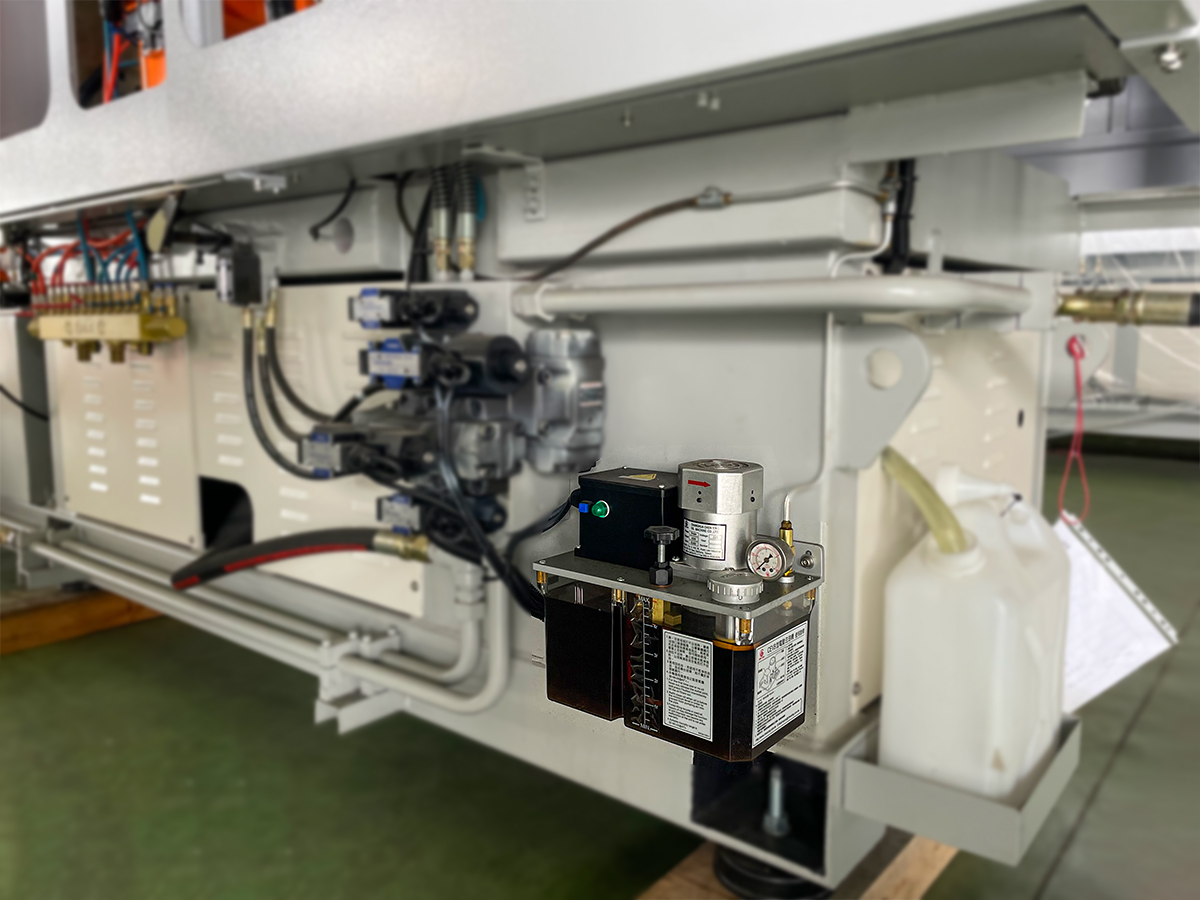
Regular Monthly Inspection Checklist
- Double-check weekly inspections more strictly and accurately.
- Check the ground wiring to see if it is well connected and whether the terminal is loosened. If the ground wiring is not well done, an accident of electric shock can occur.
- Check electric wiring to see if the entire relay is well inserted into the socket if dust/water/oil/peculiars attach the contact surface, the terminal screw is loosening or not.
- Check the moving platen and hydraulic motor slide stand to see if the slide stand is worn out or to see if the screw is loosened.
- Check the filter monthly and take it out for cleaning.
Regular Quarterly Inspection Checklist
- Double-check quarterly inspections more strictly and accurately.
- Check hydraulic oil periodically (by hydraulic oil supplier if it could be)
- Check each machine's movement to see if any parts are abnormal or worn out.
- Check the filter core quarterly and take it out for cleaning.
- Check the cooler one half a year and take it out for cleaning.
Regular Annual Inspection Checklist
- Double-check yearly inspections more strictly and accurately.
- Clean the electrical motor's inlet gap cooling part with a steel brush or air blower. Dirt or dust that gets jammed into this inlet gap can damage the motor's heating system.
- Install the ventilating windows onto the machine to check the ventilation system. This will prevent dirt and dust from entering the motor and causing overheating, which will raise the hydraulic oil temperature accordingly.
- Measure insulation to prevent electrical leakage, as electrical wrapping will become worse and worse year by year.
Proper molding machine maintenance is essential for its efficient operation and longevity. By following the maintenance checklist and guidelines in this article, you can ensure that your machine operates smoothly and consistently produces high-quality products. As an experienced injection molding machine manufacturer, we offer a complete range of injection machine models to meet our customers' needs. If you are interested in an injection molding machine, please contact Huarong.
- Group Name: Huarong Group
- Brand: Huarong, Yuhdak, Nanrong
- Service Offerings: Injection Molding Machine, Vertical Injection Molding Machine, Injection Molding Automation
- Tel: +886-6-7956777
- Address: No.21-6, Zhongzhou, Chin An Vil., Xigang Dist., Tainan City 72351, Taiwan
- Official Website: https://www.huarong.com.tw/
Previous news : Plastic Injection Molding Material Selection and Their Molding Technology
Next news: Transforming Home Appliance Manufacturing: A Success Story with Huarong's Injection Molding Machines