Plastic injection molding material selection and their Molding Technology
2024-05-09 16:24:49
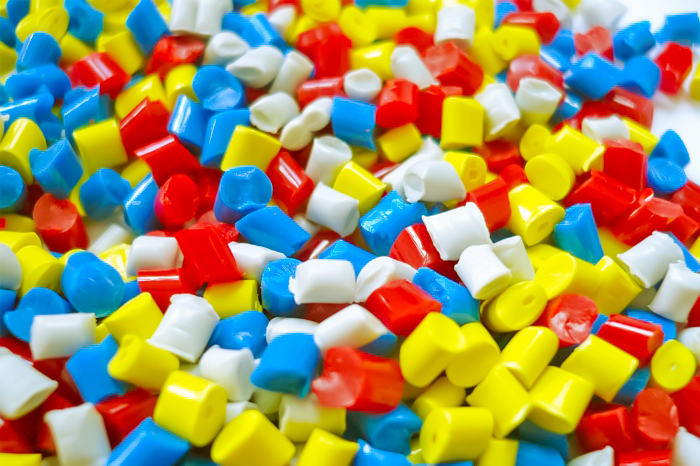
In a previous article, we talked about Understanding the 10 Most Common Injection Molding Materials. Plastic injection molding material selection is a crucial step in the injection molding manufacturing process, influencing product quality, performance, and cost-effectiveness. Choosing the right material ensures that the final product meets design requirements, withstands environmental factors, and achieves desired mechanical properties. In this article, we continue our previous article by providing you with in-depth insights into material selection and their molding technology.
When selecting a plastic material for injection molding, there are several factors to consider. These include:
- Mechanical properties: Consider the strength, stiffness, and impact resistance required for your application. Different materials have different mechanical properties, so choose one that best suits your needs.
- Thermal properties: Evaluate the material's ability to withstand high temperatures, as well as its heat resistance and thermal conductivity. This is particularly important if your product will be exposed to extreme temperatures or if it requires specific thermal properties.
- Chemical resistance: Determine the material's resistance to chemicals, solvents, and other substances that it may come into contact with during its lifetime. This has profound implications for applications where the product might be exposed to harsh chemicals or environments.
- Environmental considerations: Consider the material's biodegradability, recyclability, and environmental impact. If sustainability is a priority for your production project, choose a material that aligns with your goals.
- Cost: Evaluate the material's cost in relation to your budget. Some materials may be more expensive than others, so consider the trade-offs between cost and performance.
By carefully considering these factors, you can select a plastic material that meets the specific requirements of your injection molding project.
Further reading: Essential for Launching Your Injection Molding Business
- Acrylonitrile Butadiene Styrene (ABS)
ABS has a decomposition temperature of over 270°C, but due to factors such as time and other technical conditions, the resin often begins to discolor around 250°C. Additionally, the rubber phase in ABS is not suitable for high temperatures, as it may affect product performance. Compared to plastics like polystyrene and nylon, ABS has poorer flowability, requiring higher injection pressure. Injection pressure for ABS is not only related to factors like product wall thickness and equipment type but also influenced by the resin grade.
- Polyethylene (PE)
Polyethylene has a tendency for melt fracture during high-speed processes, but its good flowability means that moderate injection speeds are sufficient for most product molding requirements under certain injection pressures. Therefore, high-speed injection is not advisable. In the injection of polyethylene, besides ensuring appropriate injection and cooling times, sufficient packing time should also be ensured to compensate for material shrinkage issues that may lead to defects such as bubbles or indentations in the product.
- Polypropylene (PP)
Polypropylene is prone to oxidation and discoloration at high temperatures, affecting the appearance and quality of products. Therefore, the barrel temperature for polypropylene should typically be between 200-270°C. Generally, as mold temperature decreases, the crystallinity of the product decreases, resulting in increased toughness, reduced shrinkage, and decreased glossiness on the product surface. However, higher mold temperatures lead to higher product crystallinity, increased rigidity and hardness, better apparent glossiness, but may cause problems such as leakage, indentations, and increased shrinkage.
- Polystyrene (PS)
Polystyrene has a wide melting temperature range, good thermal stability, high thermal decomposition temperature (<300°C), and increased melt flowability with temperature rise. Therefore, injection temperatures can be selected between 140-260°C without degradation depending on the product. Higher injection speeds not only make it difficult to expel air from the mold cavity but also result in less smooth appearance, decreased transparency, and reduced impact strength. Thus, for PS products, lower injection speeds are preferable.
- Polycarbonate (PC)
Injection temperatures for polycarbonate are usually chosen between 271-320°C, providing a moderate melt viscosity range suitable for most products. Except for thin-walled, small-gated, deep-hole, and long-flow products, medium or slow injection speeds are generally preferred to minimize scrap and improve product quality, preferably using multi-stage injection with slow-fast-slow injection to significantly reduce scrap rate and enhance product quality.
- Poly (Methyl Methacrylate) (PMMA)
PMMA does not have a distinct melting point. The available range for molding is wide, between 160-270°C. Although the influence of injection pressure on PMMA melt flow is not as significant as injection temperature, due to its higher melt viscosity and poor flowability, higher injection pressure is still required, especially for complex-shaped or thick-walled products.
- Polyvinyl Chloride (PVC)
Molding temperatures for PVC are between 160-190°C, ideally not exceeding 200°C. During normal production, the nozzle temperature should be reduced to prevent materials from degrading and discoloring due to excessive temperatures entering the mold cavity. Due to temperature constraints and high melt viscosity, injection pressure plays a crucial role in PVC filling. Higher injection pressure reduces product shrinkage but excessive pressure may cause mold overload and product leakage, requiring careful consideration during pressure selection.
Related product: PVC - Fittings application-PVC Series
- Nylon (Polyamide, PA)
Nylon, being a crystalline material with a distinct melting point, requires different molding temperatures for different varieties, all of which should be above the crystalline melting point. Considering the poor thermal stability of nylon melts, temperatures should not be too high to avoid discoloration. While nylon has low melt viscosity and good flowability, faster cooling rates may lead to insufficient filling in complex-shaped or thin-walled products, hence requiring higher injection pressures.
- Polyoxymethylene (POM)
Generally, when the injection temperature is 20-30°C higher than the melting point, better overall physical and mechanical properties are achieved. Injection temperatures controlled between 190-200°C are ideal for obtaining products with a glossy, smooth, and bubble-free appearance. Increased injection pressure has little effect on the tensile strength of polyacetal and is beneficial for improving material flowability and product appearance without compromising mechanical properties.
- Bulk Molding Compound (BMC)
Molding temperatures are closely related to BMC flowability and the processing method of the selected molding machine. Temperatures typically range between 140-170°C. BMC materials should be stored in a cool, dark place below 18°C, and any remaining material after use should be tightly sealed. Under normal conditions, BMC can be stored for a month, but external temperatures will affect its storage life. Refrigeration can extend the life of BMC.
Related product: BMC - Bulk Molding-BMC Series
By understanding different materials' properties and molding technologies, manufacturers can optimize product performance, production efficiency, and overall profitability. Whether crafting intricate automotive components or everyday consumer goods, as an experienced injection molding machine manufacturer, Huarong can help you choose the right plastic injection molding material to set the foundation for success in the competitive landscape of plastic manufacturing. Don’t hesitate to contact Huarong.
- Group Name: Huarong Group
- Brand: Huarong, Yuhdak, Nanrong
- Service Offerings: Injection Molding Machine, Vertical Injection Molding Machine, Injection Molding Automation
- Tel: +886-6-7956777
- Address: No.21-6, Zhongzhou, Chin An Vil., Xigang Dist., Tainan City 72351, Taiwan
- Official Website: https://www.huarong.com.tw/
Previous news: What Is Overmolding? Its Process and Example vs Insert Molding
Next news: Injection Molding Machine Maintenance PDF and Checklist