Large Part Injection Molding: Techniques, Applications, and Benefits
2024-04-03 14:46:44
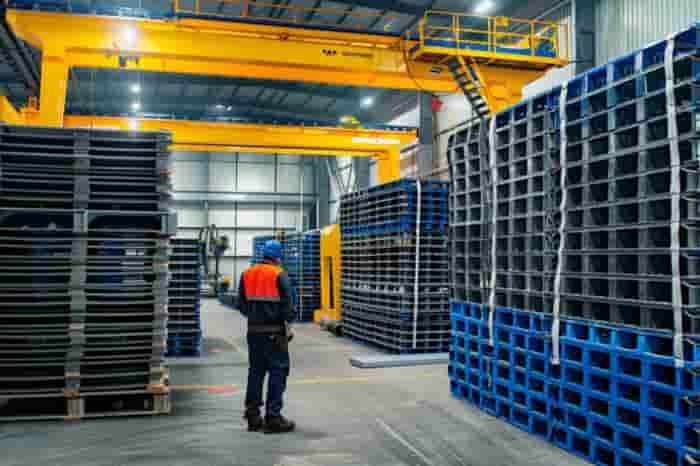
Large-part injection molding is a sophisticated manufacturing process for creating precision large-scale plastic components. This article delves into the details of this process, exploring various techniques, materials, and industry applications.
Large-part injection molding, also known as large-tonnage injection molding, shares similarities with standard injection molding but requires higher-tonnage injection molding machines (500 tons or more) to manage the increased clamping force needed for larger surface areas. Understanding the differences helps in selecting the right equipment and processes.
Large-tonnage injection molding machines are vital for producing large parts. These machines, rated by their clamping force, ensure the mold halves remain securely closed during injection. Proper tonnage calculation is crucial to prevent defects and ensure high-quality output.
Choosing the Right Equipment
Several factors must be considered when deciding whether your part requires a large-ton machine. These factors include size, material, and safety considerations. Experts recommend adding a 10% safety factor to the clamping force calculation to accommodate potential defects. Key considerations to consider are part size and complexity, material type, projected annual volume, quality requirements, mold design, and seeking expert consultation.
- Part Size and Complexity: Large parts or those with complex geometries often require higher tonnage machines to ensure adequate clamping force.
- Material Type: Certain materials, such as high-strength plastics or those with high viscosity, may require higher clamping forces to fill the mold properly.
- Projected Annual Volume: If you anticipate a high production volume, a large-ton machine may be more cost-effective in the long run due to higher efficiency and productivity.
- Quality Requirements: Parts requiring high precision or structural integrity may benefit from the stability and consistency provided by a large-ton machine.
- Mold Design: The design of your mold, including the number of cavities and the complexity of the parting line, can affect the required clamping force.
- Consultation: It's advisable to consult with injection molding experts or machine manufacturers to determine the most suitable tonnage for your specific part and production requirements.
The two-platen injection molding machine is ideal for medium—and large-sized machines. It features a unique design with two platens holding the mold halves during injection. Unlike traditional three-platen machines, this design is compact and efficient, ensuring precision and efficiency in molding large plastic products.
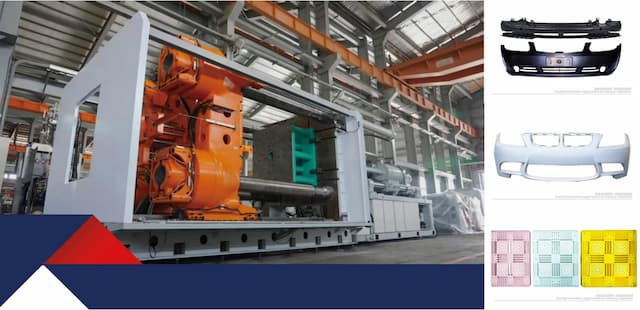
Further reading: 2 Platen Injection Molding Machine vs 3 Platen
Advantages of Two-Platen Machines for Large Parts
These machines offer cost-effectiveness, space efficiency, energy efficiency, suitability for large mold sizes, and flexibility in mold configurations. They have a smaller footprint than three-platen machines, making them ideal for limited-space environments.
- Cost-Effectiveness: These machines typically have a simpler structure and lower maintenance costs than three-platen machines, making them more economical for producing large parts in bulk.
- Space Efficiency: Two-platen machines have a smaller footprint than three-platen machines of similar tonnage. This space-saving design is particularly beneficial for manufacturers operating in limited-space environments, allowing them to maximize their production capabilities without compromising on floor space.
- Energy Efficiency: The optimized design and reduced number of moving parts result in lower energy consumption, making them a more environmentally friendly and cost-effective option for large injection molding projects.
- Suitable for Large Mold Sizes: Two-platen machines are well-suited for large mold sizes, making them ideal for producing large parts. If the mold size is compatible with a two-platen machine and the production volume justifies the investment, opting for a two-platen machine can significantly enhance production efficiency and quality.
- Flexibility: Two-platen machines offer mold sizes and configurations flexibility, allowing manufacturers to adapt to varying production requirements. This versatility makes them suitable for many large injection molding applications.
Related product: Two Platen Machine – NRH Series
Key Features of Huarong's Two-Platen Machines
Huarong's innovative approach to two-platen machine design has resulted in several patents that optimize machine efficiency and performance. Their patented technologies include the Suspended Tie-bar Bearing Module, Patented Inner Supporting Sliding Module, Patented Moving Platen Positioning Device, and Optional Patented Tie-bar Disassemble Function, which won the prestigious Taiwan Excellence Award.
Further article: HUARONG is honored with the 2024 Taiwan Excellence Award!
Gas-assisted injection molding (GAIM) is a technique that uses an inert gas, typically nitrogen, to help with the injection molding process. In GAIM, the gas is injected through air holes in the mold or the nozzle of the injection machine into the molten plastic within the mold, creating hollow sections in the part. This assists in pushing the molten plastic into the mold cavities, ensuring uniform filling and reducing internal stresses. By incorporating gas-assisted injection molding into their processes, manufacturers can achieve higher efficiency, better product quality, and reduced production costs, making it a valuable technique in large-part injection molding.
- Quality Improvement: GAIM helps produce parts with a better surface finish and reduces defects, such as sink marks and warping.
- Cycle Time Reduction: The process reduces cycle times significantly by speeding up the cooling process and reducing the amount of plastic needed.
- Weight Reduction: Finished parts are lighter because of the hollow sections created by the gas, which also reduces material costs.
Choosing the right material is crucial for the success of large part injection molding. Commonly used materials include:
- High-Density Polyethylene (HDPE): Known for its strength, chemical resistance, and recyclability, HDPE is ideal for food-safe applications.
- Acrylic (PMMA): Valued for its transparency and weather resistance, acrylic is often used in automotive and electronic components.
- Nylon (PA): This versatile material offers low friction, high abrasion resistance, and chemical stability, making it suitable for various industrial applications.
- Structural Foam: Used for lightweight, strong components, structural foam provides excellent strength-to-weight ratio and is ideal for large parts requiring durability.
Further reading: Understanding the 10 Most Common Injection Molding Materials
Large-part injection molding finds extensive applications across various industries, offering unparalleled advantages in producing oversized plastic components.
- Automotive Industry: Injection molding is pivotal in the automotive industry for manufacturing large components such as bumpers, dashboards, and door panels. The process ensures uniformity and high strength, essential for automotive safety and performance.
- Aerospace Industry: In aerospace, large part injection molding is used to produce lightweight, high-strength components like fuselages and wings. The reduced weight of plastic parts contributes to improved fuel efficiency and performance.
- Electronics Industry: The electronics industry relies on injection molding for creating durable, precise components for devices such as televisions, refrigerators, and computers. Plastic casings and structural parts are essential for protecting electronic components and ensuring device integrity.
Large part injection molding is an indispensable process in modern manufacturing, offering numerous benefits across various industries. By understanding the techniques, machinery, and materials involved, businesses can enhance their production capabilities and achieve superior product quality. As the leading plastic injection molding machine manufacturer, Huarong is committed to providing all our clients with precision, custom plastic injection molding services that deliver premium quality components. If you have any further questions or machine needs, please don't hesitate to contact Huarong.
- Group Name: Huarong Group
- Brand: Huarong, Yuhdak, Nanrong
- Service Offerings: Injection Molding Machine, Vertical Injection Molding Machine, Injection Molding Automation
- Tel: +886-6-7956777
- Address: No.21-6, Zhongzhou, Chin An Vil., Xigang Dist., Tainan City 72351, Taiwan
- Official Website: https://www.huarong.com.tw/
Previous news : Understanding the 10 Most Common Injection Molding Materials