Vertical Injection Molding vs Horizontal Injection Molding for Plastic Components
2024-03-15 16:01:59
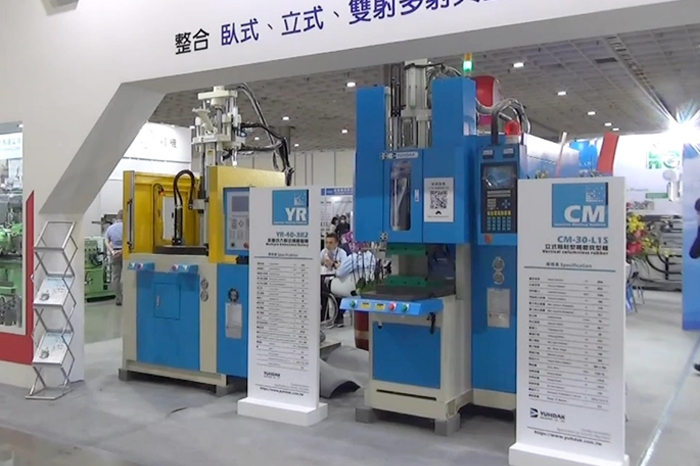
In the realm of plastic injection molding, two predominant methods reign supreme: vertical injection molding and horizontal injection molding. Both have their own advantages and are suitable for different applications. In this article, we'll explore the differences between vertical and horizontal injection molding, when to choose each method, and the key considerations for selecting the right process for your project.
Vertical injection molding operates similarly to its horizontal counterpart but with a crucial distinction: the mold halves move up and down, perpendicular to the floor. This vertical orientation excels in scenarios requiring multiple concurrent operations, such as insert molding or overmolding. Operators can find it convenient to insert objects on the horizontal surface, and if the vertical injection molding machine is equipped with a rotary table or sliding table design, the machine enables the simultaneous execution of pre- and post-molding operations while parts are being filled. This feature proves invaluable when dealing with inserts or substrates that must be loaded prior to resin injection, which can improve production efficiency.
Related product: Rotary Table Vertical Machine - YR Series
Related product: Sliding Table Vertical Machine - YH Series
Vertical injection molding offers several advantages that make it a preferred choice for specific applications during injection molding:
- Enhanced Production Efficiency: Vertical molding machines offer a more streamlined production process than horizontal machines, especially in insert molding applications. Their design allows easy part insertion into the mold, reducing the risk of misalignment and ensuring a smoother workflow.
- Space Optimization: One of the most significant advantages of vertical molding machines is their space-saving design. They typically require much less floor space than horizontal machines, making them ideal for manufacturers with limited space availability.
- Versatile Mold Tooling: Vertical machines are equipped with vertical clamp units that provide maximum flexibility in mold tooling. This allows for easy customization and adaptation to various molding needs, making them highly versatile and suitable for various applications.
- Improved Resin Flow Control: Vertical molding machines offer better control over resin flow into the mold cavity due to their vertical orientation. This results in more consistent and precise molding, reducing the likelihood of defects and improving overall product quality.
- Cost Efficiency: Vertical molding machines can be more cost-effective than horizontal machines, especially regarding material usage. The top-down injection process requires smaller runners, which means less material waste and lower production costs.
- Compact Design: Vertical machines typically have a more compact and ergonomic design than horizontal machines, making them easier to operate and maintain. This can lead to improved overall efficiency and productivity in the manufacturing process.
Vertical and horizontal injection molding are two processes used to produce plastic parts. While both methods involve injecting molten resin into a mold to form a part, they differ in several key aspects:
- Mechanism Design (Mold Orientation): The most apparent difference is the orientation of the mold. In a vertical injection molding machine, the mold halves move up and down, perpendicular to the floor. In contrast, in a horizontal injection molding machine, the mold opens and closes horizontally, parallel to the floor.
- Injection Mechanism Location: In vertical injection molding, the injection mechanism is typically positioned at the top. This allows gravity to assist in filling the mold cavity with molten resin. In horizontal injection molding, the injection mechanism is typically located on the side of the mold.
- Mold Configuration: Vertical injection molding machines often have open clamps and rotary tables, allowing for multiple molds to be used simultaneously. This can increase efficiency and productivity by enabling concurrent pre-molding, molding, and post-molding operations.
- Space and Footprint: Vertical injection molding machines typically occupy less floor space than their horizontal counterparts, making them suitable for compact production environments.
- Versatility: Horizontal machines excel in producing large volumes of parts efficiently. Conversely, vertical machines offer greater flexibility for intricate molding tasks, such as overmolding and insert molding.
- Cost: Due to their larger size, horizontal machines may require a higher initial investment, whereas vertical machines offer a cost-effective solution, particularly for specialized design applications.
When to Choose Vertical Injection Molding?
- No requirement for parts to fall from the mold: Gravity does not assist in removing parts from the open mold.
- Need for concurrent operations: Multiple molds can be used in tandem, allowing for simultaneous pre- and post-molding operations.
- Insert or overmolding requirements: Gravity aids in holding inserts in place, simplifying the molding process.
- Consistent resin flow and temperature distribution: Ensures high-quality, uniform parts.
- Space constraints: Vertical machines typically require less floor space than horizontal machines.
- Lower pressure and clamping force: Gravity helps keep the molds together during injection.
Further reading: Comprehensive Guide to Vertical Injection Molding Machines
When to Choose Horizontal Injection Molding?
- Manual part removal is needed: Gravity assists in part removal, making it suitable for manual or robotic operations.
- Multiple parts are required per cycle: Horizontal molds with multiple cavities are ideal for high-volume production.
- Parts have cylindrical shapes: Horizontal molding is well-suited for cylindrical designs.
- High production volume is required: Horizontal molding can handle large production runs efficiently.
- Inserting or over-molding is unnecessary: Horizontal molding may be more suitable for simpler part designs.
Further reading: Choosing the Right Injection Molding Machine: A Comprehensive Guide
Huarong is a trusted injection molding machine manufacturer of innovative solutions tailored to your specific manufacturing needs. Huarong ensures precision, reliability, and efficiency in every molding process with a diverse range of vertical machines. Whether in the automotive, electronics, medical, or consumer goods industry, Huarong offers customizable solutions to streamline your production and elevate your competitiveness in the market. If you have any needs for vertical injection machines, please feel free to contact Huarong.
- Group Name: Huarong Group
- Brand: Huarong, Yuhdak, Nanrong
- Service Offerings: Injection Molding Machine, Vertical Injection Molding Machine, Injection Molding Automation
- Tel: +886-6-7956777
- Address: No.21-6, Zhongzhou, Chin An Vil., Xigang Dist., Tainan City 72351, Taiwan
- Official Website: https://www.huarong.com.tw/
Previous news: What is 2K Injection Molding? 2K Molding Equipment and Advantages
Next news : What Is Insert Molding? Process, Advantages and Applications