Plastic Chair Making Machine – Complete Guide for Manufacturers
2025-05-16 08:34:07
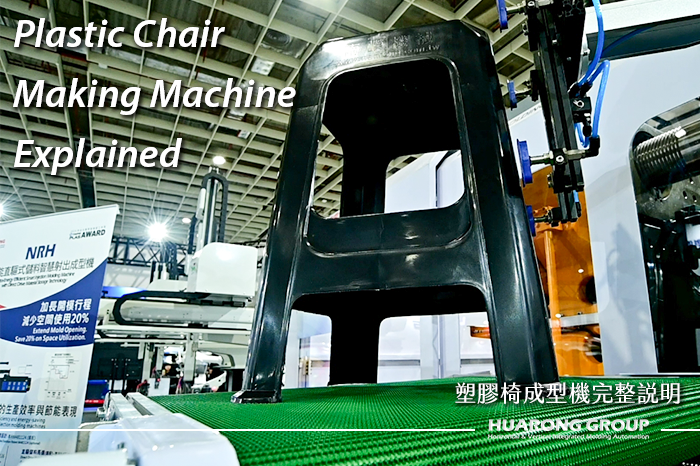
Chair making machine is a key piece of equipment used in the large-scale manufacturing of plastic chairs. These machines enable high-volume, consistent, and cost-efficient production of chairs that are used across homes, offices, schools, and public venues. This guide offers key insights into the machine, material, and manufacturing process behind plastic chair production.
A plastic chair making machine is a specialized high-tonnage injection molding machine designed to produce large, load-bearing chair products with high efficiency. These machines inject molten plastic into precision molds that shape the chair’s structure—commonly monobloc chairs, outdoor patio seats, and school furniture.
- Injection Unit: Melts and injects plastic material.
- Clamping Unit: Holds the mold closed with adequate pressure during the injection and cooling.
- Control System (PCL): Operates all process variables, including temperature, pressure, injection time, and holding pressure.
- Drive System: Hydraulic or Servo System to ensure energy efficiency and precision.
Further reading: What are Fundamentals of Injection Molding? 3 Keys to Plastic Injection Plant
A typical plastic chair mold demands a high clamping force to prevent flash, given the large surface area of the part.
Chair Type | Clamping Force Range (tons) |
---|---|
Children's Chair (Small Plastic Chair) | Approx. 250–500 tons |
Standard Household Chair (Monoblock Chair) | Approx. 600–1000 tons |
Large Outdoor Chair (Oversized Thick Chair) | Approx. 800–1300 tons |
High-end Engineering Plastic Chair (e.g., PC Material) | Approx. 800–1300 tons |
Chair Type | Shot Weight Range (grams) |
---|---|
Children's Chair (Small Plastic Chair) | Approx. 500–1500 g |
Standard Household Chair (Monoblock Chair) | Approx. 1500–3000 g |
Large Outdoor Chair (Oversized Thick Chair) | Approx. 3000–5000 g |
High-end Engineering Plastic Chair (e.g., PC Material) | Approx. 1500–3000 g |
Chair Type | Cycle Time Range (seconds) |
---|---|
Children's Chair (Small Plastic Chair) | Approx. 60–90 sec |
Standard Household Chair (Monoblock Chair) | Approx. 50–60 sec |
Large Outdoor Chair (Oversized Thick Chair) | Approx. 90–120 sec |
High-end Engineering Plastic Chair (e.g., PC Material) | Approx. 50–90 sec |
The most significant advantage is its capability to produce structurally sound, aesthetically uniform, and defect-free chairs in mass quantities. Modern chair making machines offer:
- Stable Performance during continuous high-volume operations
- Quick Mold Change to support multi-type production
- Low Scrap Rate through precision process control
- Full Automation Compatibility with robot arms and conveyor systems
- Energy Saving up to 60% using servo systems
The machine follows the injection molding cycle, optimized for chair production:
- Material Feeding: Thermoplastic granules (usually PP) are loaded.
- Plasticizing: Material melts via barrel heaters and screw rotation.
- Injection: Melt is injected into the mold at high pressure.
- Cooling: The mold cools and solidifies the chair structure.
- Ejection: The chair is pushed out via ejector pins.
- Repeat: The cycle restarts automatically.
Further reading: Injection Molding: Processes, Benefits, Applications, and Future Trends
Material selection for chair manufacturing directly affects durability, cost, and appearance.
- Polypropylene (PP)
- Lightweight, cost-effective, and easy to mold.
- Offers good stiffness and impact resistance.
- Talc-Filled or Glass-Filled Compounds
- Used for premium chairs needing extra strength.
- Requires wear-resistant screws and barrels.
- Masterbatches
- Adds UV protection and color uniformity.
- Essential for outdoor or branded chairs.
Further reading: Understanding the 10 Most Common Injection Molding Materials
Click the image to watch a full cycle of a plastic chair being manufactured to help you visualize the mold cycle and machine efficiency.
- 24/7 Production Capability
- Consistent Product Quality
- Logo Molding & Customization
- Significant Energy Savings
- Labor Reduction through Automation
Plastic chair making machines can manufacture a wide range of seating solutions:
- Monobloc chairs
- Dining chairs with armrests
- Stackable office or training chairs
- School and classroom seating
- Kids’ chairs and booster seats
- Outdoor plastic stools and patio furniture
- Public utility chairs (bus stations, railway platforms)
The optimal clamping force for producing a standard plastic chair typically falls within the 600 to 1000 tons range. However, the final tonnage selection should be based on several factors:
- Product Size and Weight: Larger or thicker chairs require higher tonnage to ensure full cavity filling and avoid flash.
- Mold Size and Projected Area: The total projected area of the mold (including runners and parting lines) determines the minimum clamping force needed to keep the mold securely closed during injection.
- Material Type: Materials with high injection pressure (e.g., PC, PC/ABS) may need higher tonnage to withstand the force.
- Multi-Cavity Mold: If producing more than one chair per cycle, a higher tonnage machine is necessary.
Yes, recycled plastic materials such as recycled PP or PE can be used in chair production, especially for economic-grade or non-load-bearing chairs. Many manufacturers adopt a blended approach, mixing recycled and virgin materials to balance cost, strength, and process stability.
However, not all materials are used in 100% recycled form, and most production lines only partially incorporate recycled content. Pure recycled plastic often lacks consistent melt flow, may contain impurities, and exhibits reduced mechanical properties, which can lead to warpage, surface defects, or even structural failure.
The lifespan of a plastic chair mold depends on several key factors:
- Mold Material:
- P20 steel molds: ~300,000 to 500,000 shots
- H13 or 2316 hardened steel molds: ~800,000 to 1,000,000+ shots
- Maintenance Practices: Regular cleaning, lubrication, and wear-part replacement can significantly extend mold life.
- Material Used: Molding abrasive or recycled materials can reduce lifespan due to increased wear.
- Cooling and Ejection Design: Well-optimized cooling and smooth ejection systems reduce stress on the mold during cycles.
The chair making machine is more than a tool—it is the engine that drives productivity, profitability, and quality in plastic chair manufacturing. Manufacturers seeking to improve efficiency, reduce energy usage, and deliver high-quality chairs consistently should invest in a machine tailored for their product range.
- Group Name: Huarong Group
- Brand: Huarong, Yuhdak, Nanrong
- Service Offerings: Injection Molding Machine, Vertical Injection Molding Machine, Injection Molding Automation
- Tel: +886-6-7956777
- Address: No.21-6, Zhongzhou, Chin An Vil., Xigang Dist.., Tainan City 72351, Taiwan