Key Role of Holding Pressure:Enhancing Yield and Stable Mass Production
2025-07-10 13:53:19
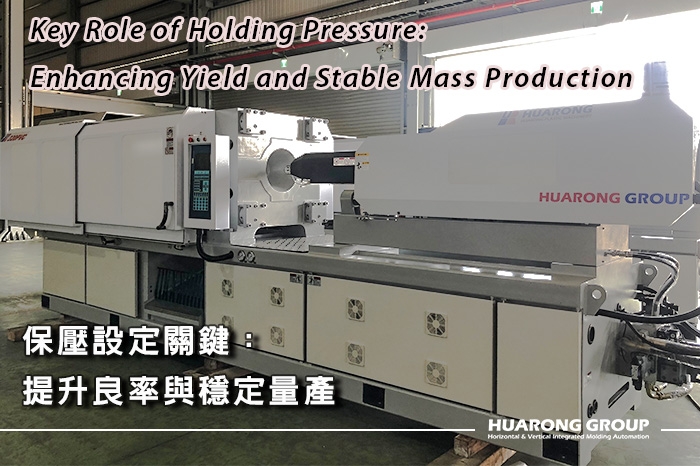
Holding pressure is often misunderstood as a secondary step following the filling phase in injection molding. In reality, it is a critical process parameter that determines the dimensional accuracy, structural density, and surface quality of molded parts. If the molding setup focuses solely on injection pressure and speed while neglecting the precision of holding pressure settings, defects such as sink marks, warpage, and internal voids may occur, ultimately reducing yield and production efficiency.
The holding phase begins after approximately 95% of the cavity has been filled, during which pressure is continuously applied to the screw to push additional melt into the cavity. This compensates for material shrinkage during cooling. Though the holding pressure is lower than the initial injection pressure, it plays a key role in dimensional stability, surface appearance, and internal density of the molded product.
- Prevents Backflow and Short Shots:Avoids melt backflow through the gate and ensures full cavity filling.
- Compensates for Cooling Shrinkage:Maintains pressure inside the mold to minimize volumetric changes.
- Improves Density and Mechanical Properties:Increases molecular packing and structural integrity.
- Suppresses Common Defects:Effectively reduces sink marks, bubbles, warpage, and internal voids.
The pressure curve in injection molding typically consists of three phases:filling, holding, and cooling. The switch from velocity-controlled injection to pressure-controlled holding must occur when the cavity is around 95% filled—this is known as the velocity-to-pressure switchover point.
If the switchover occurs too early, short shots or incomplete filling may result. If too late, it can cause flashing or mold damage due to excessive pressure. For thin-wall or high-precision parts, the switchover point is often optimized at 98% cavity fill to ensure complete filling.
Holding pressure is typically lower than the maximum injection pressure, and the appropriate value depends on the material properties, mold design, and part geometry. Below are suggested holding pressure ratios (relative to max injection pressure) for common thermoplastics:
Material | Suggested Holding Pressure Ratio |
PA (Nylon) | ≈ 50% |
POM (Polyoxymethylene) | 80% – 100% |
PP / PE (Polypropylene / Polyethylene) | 30% – 50% |
An initial holding pressure range of 1000 to 2000 psi is generally recommended. Fine-tuning should be based on actual part weight, dimensional tolerances, and appearance requirements.
Holding time must be longer than the gate freeze-off time to maintain effective pressure inside the cavity. Otherwise, issues like backflow or internal voids may occur. The most practical approach is the weight method—run several molding cycles while gradually increasing holding time. Once the part weight no longer increases, the gate is considered sealed. In general, holding time accounts for approximately 30%–40% of the total cooling time, depending on part thickness and mold temperature.
Incorrect holding parameters directly impact final part quality:
- Sink marks, especially in thicker sections.
- Internal voids or bubbles weaken structural strength.
- Short shots and incomplete filling.
- Low part density and unstable dimensions.
- Irregular molecular orientation reduces mechanical performance.
- Flashing and whitening at the gate.
- Difficult demolding or mold sticking.
- Internal stress buildup leading to warpage or cracking.
- Increased load on the clamping system reduces machine lifespan and increases energy usage.
Further reading:Common Injection Molding Defects:Causes, Types, and Solutions
To accommodate variations in cavity thickness and flow length, many modern molding processes adopt multi-stage holding pressure strategies. This approach allows for stepwise reductions in pressure and speed, resulting in smoother molding and a lower risk of defects.
- Stage 1:High pressure, low speed to fill critical zones.
- Stage 2:Medium pressure, low speed to compensate for core shrinkage.
- Stage 3:Low pressure to maintain hold and reduce pump load.
- Better control of internal stress distribution, minimizing warpage.
- Stable part dimensions and weight, especially for complex geometries.
- Protects mold inserts from displacement or damage.
- Energy savings and prolonged equipment life.
Further reading:Energy Saving Injection Molding:The Key to Lower Costs, Higher Productivity, and ESG Readiness
As smart manufacturing becomes mainstream, holding pressure control has evolved from empirical methods to data-driven dynamic optimization.
By installing pressure sensors in the mold cavity or runner system, the pressure range (100 to 3000 bar) can be monitored in real-time. The data is fed back to the injection machine controller, enabling precise identification of the gate seal point and detecting any process fluctuations.
With the integration of PLC control systems and machine learning algorithms, the system can automatically fine-tune holding parameters based on product weight, pressure curve patterns, and historical molding data. This significantly enhances stability and consistency in production quality.
Success in injection molding is not just about high-speed filling or high-pressure injection; it relies on accurate and stable control at every stage. Among them, the holding phase is essential for achieving consistent product quality and process efficiency. By mastering the correct setting of holding pressure and time, adopting multi-stage pressure strategies, and leveraging real-time data feedback, manufacturers can achieve high-quality, low-defect mass production in a sustainable and cost-effective way.
- Group Name: Huarong Group
- Brand: Huarong, Yuhdak, Nanrong
- Service Offerings: Injection Molding Machine, Vertical Injection Molding Machine, Injection Molding Automation
- Tel: +886-6-7956777
- Address: No.21-6, Zhongzhou, Chin An Vil., Xigang Dist., Tainan City 72351, Taiwan
- Official Website: https://www.huarong.com.tw/