Analysis of Short Shot Defects in Injection Molding:Causes and Solutions
2025-05-08 15:54:07
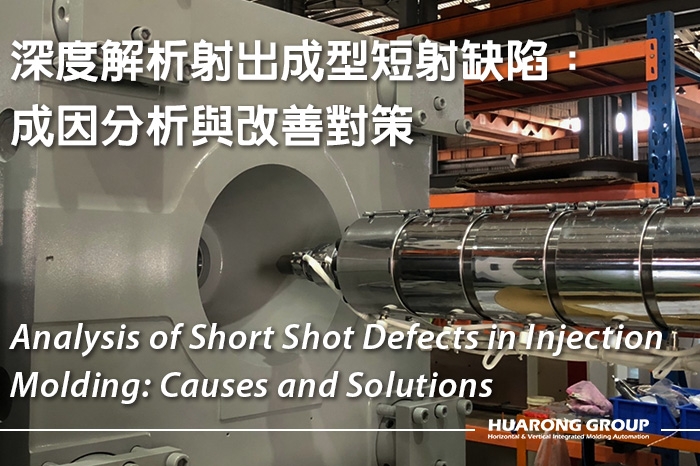
Short Shot refers to a molding defect where molten plastic fails to completely fill the mold cavity, resulting in incomplete parts, voids, or missing material on edges or internal structures. This leads to issues such as poor appearance, dimensional inaccuracies, and insufficient structural integrity. Short shots are a common yet critical issue in plastic injection molding. If not promptly resolved, they can lower product yield, increase scrap rates, and raise manufacturing costs.
Further reading: Common Injection Molding Defects: Causes, Types, and Solutions
Mold design plays a decisive role in the flow behavior of molten plastic:
- Improper runner/gate design:Undersized main runners, sub-runners, or gates can impede melt flow, increasing flow resistance and preventing full cavity filling.
- Inadequate mold venting:Trapped air in the cavity may compress and block the melt front, leading to incomplete filling in end regions.
- Uneven or low mold temperature:Low surface temperatures may cause premature solidification of the melt, reducing flowability.
- Non-uniform wall thickness:Thinner sections present higher resistance. If melt flow is insufficient, short shots are likely; local wall thickness or runner layout should be optimized.
- Unbalanced multi-cavity design:Asymmetric runner layouts can cause inconsistent fill rates and pressure across cavities, increasing the risk of localized short shots.
- Insufficient injection pressure:Pressure is the driving force behind cavity filling. If too low, the melt may stall mid-flow, leaving areas unfilled.
- Low injection speed:Inadequate velocity may cause the melt to cool prematurely and lose fluidity before reaching all cavity regions.
- Incorrect barrel or nozzle temperature settings:Underheating can lead to incomplete melting and poor flowability, while overheating may degrade the material.
- High melt viscosity:High-viscosity resins face greater resistance during flow, especially in deep or narrow areas, increasing the likelihood of short shots.
- High moisture content:Moisture turns into steam during molding, forming bubbles or expansion that disrupts consistent flow.
- Excessive regrind or additive content:Overuse of regrind or poorly mixed materials leads to inconsistent melt characteristics.
Worn screw components, faulty non-return valves, or heating malfunctions can affect injection pressure and melt delivery. Moreover, machine specifications (e.g., insufficient injection volume or mismatched tonnage) can hinder pressure control and cause short shots.
Inconsistent shear rates, unstable holding pressure, or abnormal screw retraction can result in variable shot sizes and pressures, leading to intermittent short shot defects.
- Visual inspection:Look for missing corners, voids, sink marks, or incomplete structures.
- Dimensional checks:Measure critical dimensions and compare with design specs to verify underfilling.
- Defect pattern analysis:Warping, flow marks, or poor mechanical strength may also signal short shot issues.
- Process monitoring:Track injection pressure, speed, and temperature curves to detect anomalies early.
To effectively resolve short shots, improvements should be made across mold design, processing parameters, raw material handling, and machine condition:
- Revise runner and gate dimensions:Increase size to reduce pressure drop and enhance flow efficiency.
- Enhance mold venting:Add venting grooves or utilize ejector mechanisms for better air release.
- Increase mold temperature:Use mold temperature controllers to maintain ideal conditions and improve flow stability.
- Increase injection pressure and speed:Adjust based on product geometry and flow distance to overcome resistance.
- Extend packing and fill times:Allow enough time for full filling and cooling to reduce shrinkage and underfilling.
- Verify proper temperature settings:Adjust barrel, nozzle, and mold temperatures according to resin properties to ensure optimal flow.
- Use low-viscosity, high-MFI resins:For complex or fine-detail parts, select materials with better flow characteristics.
- Ensure thorough drying:Use a dehumidifying dryer and follow appropriate temperature/time guidelines to reduce moisture content.
- Maintain consistent material sourcing and formulation:Avoid batch inconsistencies or excessive regrind that may alter melt behavior.
- Regularly check screw, non-return valve, and heaters to ensure proper function.
- Match machine capacity to product and mold size, especially injection volume and clamping force.
- Utilize monitoring systems (e.g., pressure sensors, screw position feedback) for real-time diagnostics and anomaly detection.
Effectively addressing short shot defects requires thorough technical analysis and cross-functional collaboration among mold designers, process engineers, and material suppliers. Only by optimizing designs from the outset and integrating precise machine settings with controlled material management can manufacturers achieve complete cavity filling, stable quality, and improved injection molding productivity.
- Group Name: Huarong Group
- Brand: Huarong, Yuhdak, Nanrong
- Service Offerings: Injection Molding Machine, Vertical Injection Molding Machine, Injection Molding Automation
- Tel: +886-6-7956777
- Address: No.21-6, Zhongzhou, Chin An Vil., Xigang Dist.., Tainan City 72351, Taiwan