PET Preform Production Line Planning Guide: From Bottle Buyer to In-House Manufacturing
2025-05-02 09:53:27
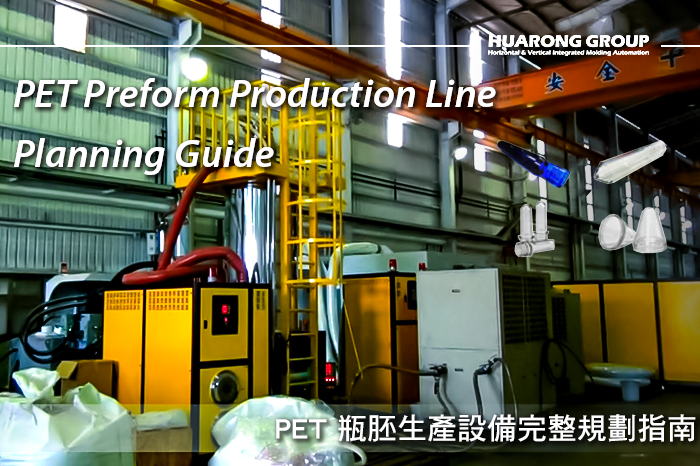
With the booming demand and competition in the bottled water market, more manufacturers are shifting from buying ready-made bottles to producing PET preforms. However, transitioning from a bottle buyer to a PET preform producer requires careful planning: What equipment is needed? How should you plan your production capacity? What hidden factors must you consider? In this comprehensive guide, we will walk you through every step to confidently build your first PET preform production line.
To be a PET preform manufacturer that establishes a complete PET preform production system, you will need the following core equipment:
- PET Injection Molding Machine
- PET Dehumidifying and Drying System
- PET Bottle Preform Mold
- Mold Dehumidifier
- Water-Cooled Chiller
The injection molding machine is the core of PET preform production. It melts PET pellets and injects them into the mold cavity to form preforms. We recommend using PET-specific injection molding machines, optimized for high plasticizing capacity and stable shot control.
Key Features:
- Equipped with PET-dedicated screws for low shear and high plasticizing efficiency
- High injection volume to support multi-cavity molds
- Designed for fast cycle times and precise control
PET is highly hygroscopic. Excess moisture can cause polymer degradation, resulting in haziness, brittleness, discoloration, and a reduction in molecular weight. Proper drying before injection is critical.
- Dehumidifier Main Unit
- Supplies stable, low dew point air (as low as -40°C)
- Uses rotary honeycomb technology for efficient moisture removal
- Drying Hopper
- Double-layer stainless steel construction for thermal insulation
- Designed for uniform heating to ensure consistent moisture levels
- Vacuum Loader
- Automatically transfers PET pellets to the hopper or injection machine
- Fully enclosed to prevent moisture reabsorption
- Mold Dehumidifier
- Keeps the mold environment dry
- Prevents condensation on mold surfaces, protecting product transparency and mold life
- Water-Cooled Chiller
- Supplies consistent cooling to mold, oil circuits, and drying units
- Enhances cycle time and preform dimensional stability
- Filters: Protect the system from air impurities
- Dew Point Monitor: Real-time dew point tracking for process control
- Drying Temperature: 160–170°C
- Drying Time: Minimum 4 hours
- Target Moisture:<50 ppm after drying
- Maintenance: Regular filter and monitor checks are essential for long-term stability
The mold defines the shape, thread type, wall thickness, and weight of each preform, directly impacting the final bottle quality.
- Product Characteristics: PET preforms are intermediate products designed for secondary processing. They resemble miniature bottles, complete with a threaded neck and a sealed bottom. As preforms undergo blow molding in the next stage, each preform must maintain highly consistent dimensions and weight to ensure uniform bottle quality after blowing.
- Cavity Count and Productivity: To meet the demands of mass production, PET preform molds are typically designed with multiple cavities—commonly 24, 48, or even up to 144 cavities—which enable simultaneous molding and significantly increase output capacity.
- Runner System Design: Almost all PET preform molds adopt a hot runner system, usually paired with valve gate nozzles. This setup ensures that the molten PET material is evenly distributed into each cavity while minimizing cold slugs and flash, thereby reducing material waste.
- Cooling Requirements: PET materials have specific cooling requirements during the preform molding process. To prevent crystallization and cloudiness caused by slow cooling, PET molds are equipped with complex and efficient internal cooling channels that allow thick-walled preforms to cool quickly and uniformly.
- Note: In addition to internal mold cooling, many PET preform production lines also adopt external cooling solutions. After demolding, robotic arms transfer the still-warm preforms to dedicated external cooling stations. This quickly dissipates residual heat from the preform’s core, further stabilizing shape and clarity.
- Demolding Considerations: Since the threaded neck of the PET preform is part of the final bottle, the demolding mechanism must be carefully designed to protect the threads. PET preform molds often use automated unscrewing systems or slider-based parting mechanisms to ensure the threads are safely released during mold opening, avoiding damage from forced ejection.
Equipment | Function Summary | Impact on Production |
---|---|---|
PET Injection Molding Machine | Melts and injects PET into the mold. Should feature high plasticizing efficiency and PET screws. | Preform dimensional stability, production speed |
PET Drying System | Removes moisture to prevent defects like haze or brittleness | Transparency, crystallization control, material quality |
PET Preform Mold | Multi-cavity hot runner design with efficient cooling and consistent threads | Preform uniformity, cooling time, blow molding consistency |
Mold Dehumidifier | Keeps mold surfaces dry in high-humidity environments | External appearance, mold durability |
Water-Cooled Chiller | Supplies cooling water for mold, oil, and dryer | Cooling consistency, reduced cycle time |
After finalizing your equipment list, the next step is to match machine capacity with your monthly production goals.
- Set Monthly Production Target
Estimate the number of preforms you need each month. For instance, if your bottling line fills 10,000 bottles/day (1 shift), your monthly preform requirement is ~300,000 pcs. - Calculate Single Machine Output
Example: A 24-cavity mold with a 20-second cycle time produces approximately 4,320 preforms per hour. If the machine runs 20 hours a day, it yields approximately 86,400 pieces a day or around 2.59 million per month (assuming 100% uptime). Realistically, use 80% for planning. - Decide Number of Machines or Cavities
Compare machine output with the target volume. One machine may suffice with room to scale. Consider multiple machines or higher cavity molds for large targets (e.g., 10M/month) - Choose the Right Machine Model
Clamping Force: Estimate ~5 tons per cavity (e.g., 48-cavity needs ~240T)
Injection Volume: Multiply preform weight × cavity count to calculate shot size
Example: 30g × 24 = 720g → machine should support >750g shot size - Plan for Future Growth
Consider installing scalable systems or purchasing a larger machine initially to accommodate cavity expansion or the later installation of a second machine.
- Match the clamping force to cavity count.
- Ensure the shot size accommodates the total mold volume
- Choose based on PET consumption per hour (kg/hr)
Weight | Wall Thickness | Cavity | Injecton Molding Machine (*) | |
---|---|---|---|---|
PCO1881 | 32 | 2.8 | 48 | 620PETFC |
PCO1881 | 29 | 2.5 | 72 | |
38mm Bericap | 28 | 2.7 | 48 | 420LLPETFC |
PCO1881 | 20.5 | 2.5 | 48 | |
PCO1881 | 35.5 | 3.7 | 48 | |
PCO1810 | 21 | 2.4 | 48 | |
PCO1881 | 44 | 3.8 | 32 | 320LLPETFC |
PCO1810 | 29 | 3.3 | 32 |
Building a PET preform production line may seem complex, but with a clear understanding of each piece of equipment’s role, you can create a highly efficient and scalable system. This guide is designed to provide a clear, practical roadmap for setting up your PET preform production operation.
- Group Name: Huarong Group
- Brand: Huarong, Yuhdak, Nanrong
- Service Offerings: Injection Molding Machine, Vertical Injection Molding Machine, Injection Molding Automation
- Tel: +886-6-7956777
- Address: No.21-6, Zhongzhou, Chin An Vil., Xigang Dist.., Tainan City 72351, Taiwan