Automotive Injection Molding: Process, Benefits, and Key Applications
2025-01-23 09:04:37
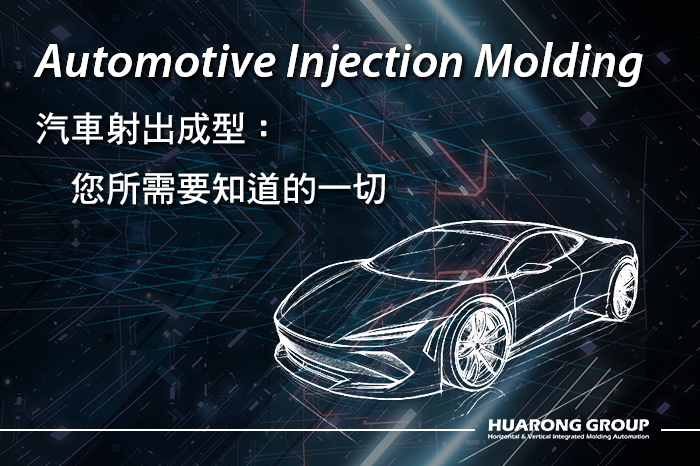
Automotive injection molding ensures that each part is virtually identical to the next, maintaining high consistency across large production runs. This repeatability is crucial in the automotive industry, where uniformity directly impacts vehicle performance and safety. Besides, it plays a key role in creating high-quality components for modern vehicles, including interior elements like dashboards and exterior parts like bumpers. This guide highlights the key processes, materials, benefits, and innovations in injection molding shaping the automotive industry's future.
Automotive injection molding is a manufacturing process where molten plastic is injected into a mold cavity, forming parts such as dashboards, bumpers, and interior trims. This method allows for creating complex shapes with high precision, making it indispensable in automotive manufacturing.
Related product: Automation in Injection Molding - Manipulator Arm
1. Repeatability and Consistency
Injection molding ensures that each part produced is virtually identical to the next, maintaining high consistency across large production runs. This repeatability is crucial in the automotive industry, where uniformity directly impacts vehicle performance and safety.
2. Cost-Effectiveness for Mass Production
While the initial investment in mold creation can be substantial, injection molding becomes highly cost-effective for large-scale production. As production volumes increase, the per-unit cost decreases, making it an economical choice for manufacturing millions of parts.
3. Material Versatility
The process accommodates various thermoplastic and thermosetting polymers, allowing manufacturers to select materials that meet specific mechanical and thermal requirements. Commonly used plastics include polypropylene (PP), acrylonitrile butadiene styrene (ABS), polyamide (PA), and polycarbonate (PC).
4. High Precision and Quality for Surface Finish
Injection molding produces parts with tight tolerances and excellent surface finishes, reducing the need for additional machining or finishing processes. This precision is essential for components that require exact dimensions and smooth surfaces.
5. Design Flexibility
The process allows for complex geometries and intricate designs, integrating multiple functionalities into a single part. This flexibility supports innovative automotive designs, reduces weight, and simplifies assembly.
6. Durability
Injection-molded parts are designed to withstand the demanding conditions of automotive applications, including high temperatures, mechanical stresses, and chemical exposure. This durability ensures that components maintain their integrity and performance over the vehicle's lifespan, reducing the need for frequent replacements and enhancing overall reliability.
Here are some commonly used materials:
Material | Properties and Applications |
---|---|
Polypropylene (PP) | Lightweight, chemical-resistant; used in interior components and under-the-hood parts |
Acrylonitrile Butadiene Styrene (ABS) | High impact resistance and good mechanical properties; used in dashboards and trim components. |
Polyamide (PA) or Nylon | High strength and thermal resistance are used in engine covers and air intake manifolds. |
Polycarbonate (PC) | Excellent toughness and clarity; used in light housings and lenses. |
Further reading: Understanding the 10 Most Common Injection Molding Materials
- Material Preparation: Plastic pellets are dried to eliminate moisture that could affect quality.
- Melting: The dried pellets are heated in a barrel until they reach a molten state.
- Injection: The molten plastic is injected into a custom-designed mold under high pressure, ensuring it fills every cavity.
- Cooling: The mold is cooled, solidifying the plastic into the desired shape.
- Ejection: Once solidified, the finished part is ejected from the mold and ready for any necessary post-processing.
Further reading: What is Injection Molding? Processes, Benefits, and Applications
Exterior Components
- Bumpers: Engineered to absorb impact and enhance vehicle safety.
- Grilles: Molded for optimal airflow and front-end protection.
- Side Mirrors: Manufactured for durability and aerodynamic design.
Interior Components
- Dashboard Panels: Precisely crafted to house instruments and controls.
- Door Handles and Trim: Designed for both functionality and aesthetic appeal.
- Center Consoles: Created to integrate storage solutions and electronic interfaces seamlessly.
Engine Components
- Engine Covers: Designed to protect critical engine parts and minimize noise.
- Air Intake Manifolds: Molded for efficient airflow management to the engine.
- Battery Housings: These are produced to enclose and protect automotive batteries securely.
Lighting Components
- Headlight Housings: Molded to provide robust protection for lighting elements.
- Tail Light Enclosures: Designed for durability and precise light dispersion.
- Signal Light Covers: Crafted to ensure clarity and resistance to environmental wear.
Groundbreaking advancements in techniques, materials, and technology integration define the future of injection molding in automotive manufacturing. Innovations such as thin-wall and microcellular injection molding enable manufacturers to achieve unprecedented levels of lightweight and efficiency. In contrast, reaction injection molding (RIM) supports the production of flexible, large-scale components. The industry's sustainability drives the adoption of recycled and bio-based plastics, aligning with circular economy goals.
1. Thin-Wall Injection Molding
This technique focuses on producing parts with reduced wall thickness, leading to material savings and shorter cycle times. It's particularly beneficial for manufacturing lightweight components that contribute to overall vehicle weight reduction.
2. Microcellular Injection Molding
Also known as microcellular foam molding, this process creates parts with a cellular structure, reducing weight while maintaining structural integrity. It's advantageous for producing lightweight, high-strength components.
Related reading: Microcellular Foam Injection Molding: Achieving Maximum Weight Reduction and Dimensional Stability
3. Reaction Injection Molding (RIM)
RIM involves mixing two reactive materials that cure within the mold, producing lightweight and flexible parts. It's commonly used for significant automotive components like bumpers and fenders.
4. Increased Use of Recycled and Bio-Based Plastics
The shift toward sustainability has spurred the adoption of recycled and bio-based plastics in injection molding. Automotive manufacturers leverage materials like recycled polypropylene and polylactic acid (PLA) to reduce environmental impact. These materials meet stringent performance requirements while supporting circular economy initiatives.
5. Smart Manufacturing: Leveraging Industry 4.0 Technologies
Industry 4.0 integration revolutionizes injection molding with real-time monitoring, predictive maintenance, and process optimization. Advanced sensors and software enable data-driven decision-making, improving production efficiency and ensuring consistent quality. This approach is pivotal for meeting the precision and scalability demands of automotive manufacturing.
6. Integration with Electric Vehicle (EV) Production
Injection molding is increasingly tailored to meet the specific needs of EV production. Components such as battery enclosures, lightweight structural elements, and thermal management parts are being designed with advanced polymers and composites to support EV efficiency and durability. This innovation aligns with the growing demand for electric and hybrid vehicles.
Selecting an experienced injection molding machine manufacturer is critical to achieving high-quality results. Consider the following when choosing a supplier:
- Expertise and Experience: Look for a company with a proven track record in automotive injection molding.
- Equipment and Technology: Ensure they use advanced machinery to handle your specific requirements.
- Quality Assurance: A strong quality control system ensures consistent results and compliance with industry standards.
- Customization Options: A reliable partner should offer design and material customization to meet unique project needs.
As the automotive industry moves toward electrification and sustainability, injection molding is expected to play a pivotal role in:
Lightweighting and Sustainable Materials
The automotive industry increasingly focuses on sustainability, developing lighter components to improve vehicle efficiency and range, biodegradable polymers, and recycling-friendly designs.
Electric and Servo Injection Molding Machines
The industry is transitioning from traditional hydraulic machines to electric and hybrid models. Electric injection molding machines (EIMMs) offer higher energy efficiency, faster cycle times, and improved precision, making them suitable for complex and delicate automotive parts. Servo machines, combining electric and hydraulic technologies, offer a balance of power and efficiency, particularly for significant automotive components.
Related technology: Power Unit > Servo System
Industry 4.0 Integration
With the adoption of Industry 4.0 technologies, injection molding machines are now equipped with sensors and software for real-time monitoring and data analysis. This integration enables predictive maintenance, enhances production efficiency, and ensures consistent quality. Smart factories leveraging these technologies are poised to set new standards in automotive manufacturing.
Related product: Smart Factory Management - HFM
Automotive injection molding is at the forefront of modern manufacturing. It enables the production of high-quality, lightweight, and cost-effective components that meet the automotive industry's rigorous standards. By leveraging advanced materials, cutting-edge technologies, and sustainable practices, manufacturers can stay ahead in a competitive market.
Whether you're a manufacturer exploring new opportunities or a designer aiming to push boundaries, injection molding offers the versatility and reliability needed to turn your vision into reality.
- Group Name: Huarong Group
- Brand: Huarong, Yuhdak, Nanrong
- Service Offerings: Injection Molding Machine, Vertical Injection Molding Machine, Injection Molding Automation
- Tel: +886-6-7956777
- Address: No.21-6, Zhongzhou, Chin An Vil., Xigang Dist., Tainan City 72351, Taiwan
Previous news : How to Repair an Injection Molding Machine: A Step-by-Step Guide
Next news: Enhancing Efficiency and Sustainability: New Solutions for Thermoplastic Injection Molding