大理石纹注塑成型技术:工艺、混色注塑机与应用
2025-03-14 09:27:40
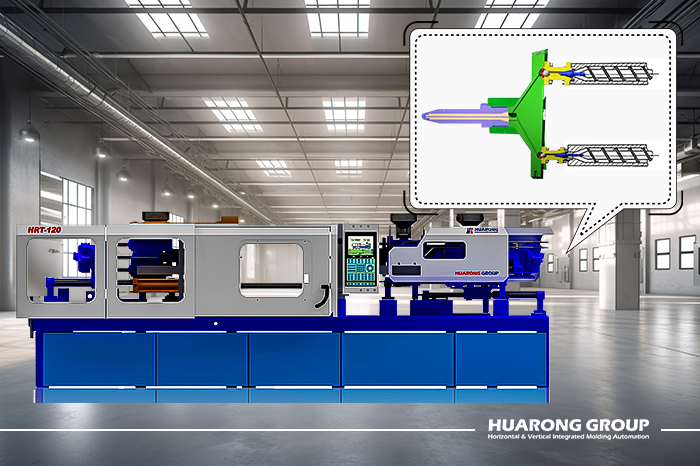
在塑胶注塑成型领域,实现独特且具有视觉冲击力的表面花纹越来越重要。 「大理石纹注塑成型技术」是一种专业的注塑工艺,能够在塑胶制品内部创造出漩涡状、条纹状或混色效果,使产品具备高级的美感,这项技术广泛应用于消费电子、汽车零件及装饰塑胶产品,以提升产品的市场区隔与竞争优势。
大理石纹注塑成型技术是透过精确控制,将两种或多种不同颜色的塑胶材料注入模具内,形成自然混合、漩涡或条纹效果。与传统的双色射出成型相比,此技术不会产生明显的颜色分界,而是使颜色动态融合,形成独特且不可预测的纹理。该技术让制造商能够在不需额外后加工的情况下,实现类似大理石的自然纹路,使其成为一种兼具成本效益与美观性的解决方案。
影响大理石纹图案的因素
要达成稳定且美观的大理石纹效果,需考量以下关键参数:
- 注塑顺序与时间控制:材料的注射顺序对最终外观影响极大。同步注塑能产生较均匀的混合效果,而依序射出则会形成分层或渐变的颜色图案。
- 注塑速度与压力:速度与压力的变化会影响颜色的混合方式。较快的速度可产生细致的条纹,而较慢的速度则可能导致较粗的纹理。
- 共射模头与模具设计:模具内部的流道配置决定材料在进入模穴前如何混合。此外,模具的肋厚、进胶点位置与流道设计都会影响塑胶的流动方式,进而改变最终的纹理呈现。共射模头决定材料在进入模具之前如何合并。此外,模具特征(例如肋厚度、浇口位置和流道)会引导塑胶移动,从而影响最终的图案。
- 材料相容性与流动特性:材料的黏度、熔融温度与流动行为都会影响其混合方式。流动性相近的材料可形成较平滑的颜色过渡,而流变性差异较大的材料则能创造出更鲜明的纹理。
该技术利用多射出系统,透过特别设计的流道与喷嘴系统,将两种注塑成型塑料依照设定的顺序或同步注入模穴中,进而产生不同的大理石纹效果,例如混合、分层渐变或条纹颜色。
1. 机台配置
为了实现大理石纹注塑效果,混色注塑成型机配置为:
- 两个独立的注射单元,允许精确控制不同材料或颜色。
- 专门设计的共射模头设计,通过内部通道和阀门机制引导材料流动,控制熔融塑料进入模具腔时的相互作用。
2. 共射模头功能
控制两种材料在注入模具腔时的混合方式至关重要。
- 注塑顺序控制: 决定第一种材料是否在第二种材料之前进入模具,或者它们是否同时注入。
- 注塑速度和压力调整: 改变塑料的流动行为,影响混合程度和纹理形成。
3. 大理石纹效果的注塑顺序
最终的大理石纹图案通过调整材料进入的时机和顺序来确定。可以实现不同的视觉效果:
注塑模式 | 描述 | 结果图案 |
---|---|---|
同时注塑 | 两种材料同时注入 | 两种材料同时注入模具,混合效果较为均匀,适合创造自然的大理石纹理 |
顺序注塑 (第一射注塑 → 第二射注塑) | 第一次注射填充部分模具,然后注入第二种材料 | 先注入一种材料填充部分模具,再注入第二种材料,适合创造分层或渐变颜色效果 |
交替注射 (第一射注塑 → 第二射注塑 → 再次第一射注塑) | 材料交替注入模具腔中 | 材料交替注入模具腔中,适合创造复杂的漩涡或波浪状纹理,图案更具动态感 |
4. 大理石纹效果的材料选择
双色注塑可以涉及:
- 相同塑料材料的不同颜色(例如黑色PP + 白色PP)→ 产生渐变或混合颜色效果。
- 不同塑料材料和颜色(例如ABS + PMMA,或PP + TPE)→ 不仅影响外观,还影响质感、耐用性或抓握性能(例如,刚性外壳与软触感层)
5. 模具设计的影响
模具结构,包括肋厚度、流道和浇口位置,影响塑料在腔内的流动和混合方式。适当的设计调整可以优化大理石纹效果,同时保持一致性。
优势
- 独特的视觉吸引力,适合定制设计–每个产品都有独特的大理石纹图案,增强设计美感。
- 无需后处理–消除了额外的印刷、喷涂或涂层需求。
- 广泛的应用–适用于多个行业,包括汽车、电子、包装和家居装饰。
挑战
- 图案可重现性–由于动态混合,在大规模生产中实现完全相同的图案较为困难。
大理石纹注塑成型虽非新技术,但随着市场对于高端视觉效果的需求增加,越来越多企业开始采用此技术,以提升产品的独特性与市场吸引力。透过双色注塑成型机、精确的共射模头设计与材料最佳化选择,制造商可生产出具高度视觉冲击力且高价值的塑胶产品。
寻找最佳的大理石纹注塑成型解决方案?
华嵘专注于高效能混色注塑成型机,能够精确控制大理石纹效果,确保稳定的生产品质与高效制程。欢迎与我们联系,探讨最适合您的注塑成型技术解决方案!
- 集团名称: 华嵘集团
- 品牌: 华嵘、煜达、南嵘
- 服务项目: 注塑机、立式射出机、成型设备取出装置
- 服务电话: (06)7956777
- 集团总部: 台南市西港区庆安里中州21之6号
- 官方网站: https://www.huarong.com.tw/
前一则新闻:客制化注塑机:为何标准机型无法满足现代制造需求?