保压设定关键:提升良率与稳定量产
2025-07-10 13:53:19
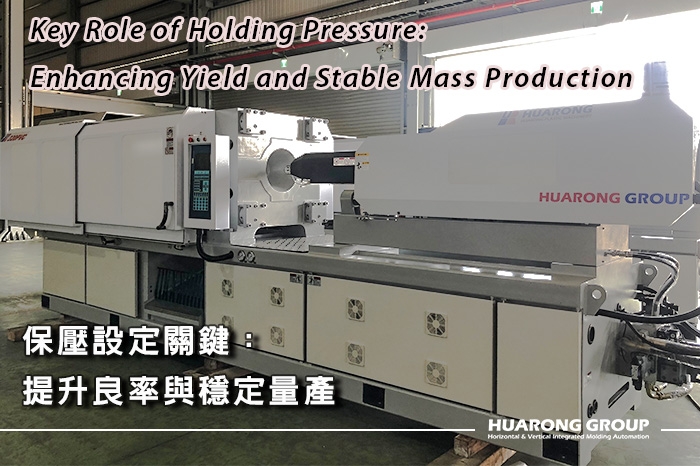
保压(Holding Pressure)在注塑成型中往往被误认为是填充后的辅助程序,但实际上,它是确保产品尺寸稳定、结构密度与外观质量的关键控制参数。如果成型条件仅注重注射压力与速度,而忽略保压设定的精准性,可能导致缩水、翘曲、内部空隙等严重缺陷,进一步影响良品率与生产效率。
保压是指在模腔几乎填满(约95%)之后,持续对螺杆施加压力,使熔胶继续推进至模腔内,以补偿材料在冷却过程中的体积收缩,此阶段压力虽低于初始注塑压力,但对成品尺寸稳定性、表面外观与内部结构密度具有关键影响。
- 防止回流与短射:避免熔胶经由浇口回吸,导致填充不足
- 补偿冷却收缩:维持模腔内的压力,有效抑制体积变化
- 提升密度与机械性能:提高结晶密度与结构稳定性
- 抑制成型缺陷:有效减少缩水、气泡、翘曲与内部空洞等问题
压力曲线在注塑成型中通常分为三个阶段:填充、保压与冷却,当模腔约填满95%时,应将注塑机的控制模式由速度控制切换为压力控制,这个关键转换点称为压力切换点(Velocity-to-Pressure Switchover)。
若转换过早,会导致模腔填充不足产生短射;若转换过晚,则可能因压力过高产生毛边或模具损伤,对于薄壁或高精密件,建议可将切换点提高至模腔填充的98%,以确保充模完整性。
保压压力通常低于最大注射压力,实际数值依据材料特性、模具设计与制品结构而定,以下为常见热塑性塑料的建议保压比(相对于最大注射压力):
材料 | 建议保压比 |
PA(尼龙) | 约 50% |
POM(聚甲醛) | 80% ~ 100% |
PP / PE(聚丙烯 / 聚乙烯) | 30% ~ 50% |
初步建议将保压压力设定在 1000 至 2000 psi 范围内,并根据实际产品重量、尺寸公差与外观要求,进行逐步微调以达成最佳成型条件。
保压时间应至少长于浇口的封闭时间,否则模腔内的压力将无法有效维持,导致回吸与内部空洞,常见做法为称重法—— 连续成型多件产品,逐步延长保压时间,当制品重量不再增加时,即可判断浇口已封闭。实务上,保压时间约占整体冷却时间的 30% ~ 40%,视产品厚度与模温而定。
设定不当的保压参数将直接影响产品质量:
- 出现缩水,尤其在厚壁区域更为明显
- 内部气泡或空洞,导致结构强度不足
- 短射与填充不完整
- 制品密度不足、尺寸不稳定
- 分子排列异常,影响机械强度与使用寿命
- 毛边与浇口发白
- 模具脱模困难或产生黏模现象
- 模内应力积累,导致翘曲或开裂
- 设备负载增加,影响锁模寿命与能耗
延伸阅读:注塑成型缺陷:原因及解决方案
为克服不同模腔厚度与流动长度对压力需求的差异,许多现代成型制程采用多段保压策略,此方法可分阶段降低压力与速度,使成型过程更为平稳、缺陷风险更低。
- 第一段:高压低速,稳定填充关键区域
- 第二段:中压低速,补偿主体收缩
- 第三段:低压维持,减少泵浦负载与能耗
- 控制内应力分布,降低变形与翘曲
- 稳定复杂制品的尺寸与重量
- 保护模内嵌件,避免位移损坏
- 节能降耗,提高设备寿命
随着智能制造趋势兴起,保压控制已由传统经验法则,迈向数据驱动的动态优化。
通过在模腔或流道内部安装压力传感器,可实时追踪压力变化范围(100 ~ 3000 bar),并将数据回传至注塑机控制界面,有效掌握浇口封固点与每次成型波动。
通过引入PLC控制系统与机器学习算法,系统可依据产品重量、压力曲线与历史记录,自动修正保压参数,大幅提升保压设定的稳定性与生产质量一致性。
注塑成型的成功并不只依赖高速充填与高压驱动,而是在于每一阶段精准而稳定的控制。其中,保压阶段的参数设定与监控技术,是决定产品一致性与制程效率的关键,唯有掌握正确的保压压力与时间设定原则,搭配多段保压策略与实时数据反馈技术,才能真正实现高品质、低缺陷的注塑量产。
- 集团名称: 华嵘集团
- 品牌: 华嵘、煜达、南嵘
- 服务项目: 注塑机、立式射出机、成型设备取出装置
- 服务电话: (06)7956777
- 集团总部: 台南市西港区庆安里中州21之6号
- 官方网站: https://www.huarong.com.tw/