保壓設定關鍵:提升良率與穩定量產
2025-07-10 13:53:19
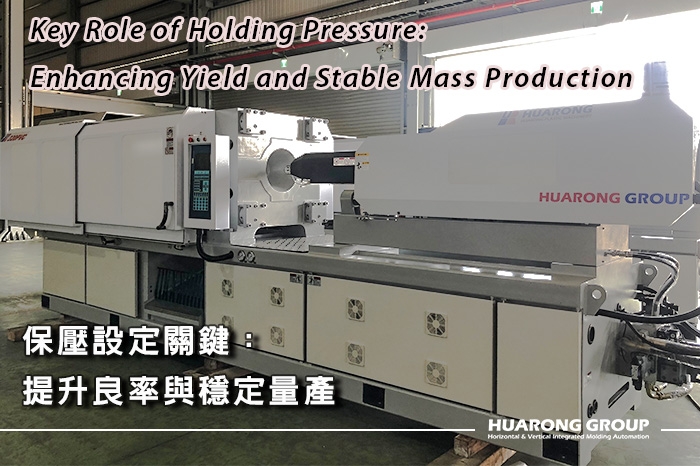
保壓(Holding Pressure)在射出成型中往往被誤認為是填充後的輔助程序,但實際上,它是確保產品尺寸穩定、結構密度與外觀品質的關鍵控制參數。若成型條件僅著重射出壓力與速度,而忽略保壓設定的精確性,將可能導致縮痕、翹曲、內部空隙等嚴重缺陷,進一步影響良率與生產效率。
保壓是指在模穴幾乎填滿(約95%)之後,持續對螺桿施加壓力,使熔膠持續推進至模穴內,補償材料在冷卻過程中的體積收縮,此階段壓力雖低於初始射出壓力,卻對成品尺寸穩定性、表面外觀與內部結構密度具有關鍵影響。
- 防止回流與短射:避免熔膠經由閘口回吸,導致填充不足
- 補償冷卻收縮:維持模穴內的壓力,有效抑制體積變化
- 提升密度與機械性質:提高結晶密度與結構穩定性
- 抑制成型缺陷:有效減少縮痕、氣泡、翹曲與內部空洞等問題
壓力曲線在射出成型中通常分為三個階段:填充、保壓與冷卻,當模穴約填滿95%時,即應將射出機的控制模式由速度控制轉為壓力控制,這個關鍵轉換點稱為壓力轉換點(Velocity-to-Pressure switchover)。
若轉換過早,會導致模穴填充不足產生短射;若轉換過晚,則可能因壓力過高產生毛邊或模具損傷,對於薄壁或高精密件,建議可將轉換點提高至模穴填充的98%,以確保充模完整性。
保壓壓力通常低於最大注射壓力,實際數值依材料性質、模具設計與成品結構而定,以下為常見熱塑性塑料的建議保壓比(相對於最大注射壓力):
材料 | 建議保壓比 |
PA(尼龍) | 約 50% |
POM(聚甲醛) | 80% ~ 100% |
PP / PE(聚丙烯 / 聚乙烯) | 30% ~ 50% |
初步建議將保壓壓力設定於 1000 至 2000 psi 範圍內,並根據實際產品重量、尺寸公差與外觀需求,進行逐步微調以達最佳成型條件。
保壓時間應至少長於閘口的封閉時間,否則模穴內的壓力將無法有效維持,導致回吸與內部空隙,常見作法為使用稱重法 —— 連續成型多件產品,逐步延長保壓時間,當重量不再增加時,即可判定閘口已封閉。實務上,保壓時間約占整體冷卻時間的30% ~ 40%,視產品厚度與模溫而定。
設定不當的保壓參數將直接影響產品品質:
- 產生縮痕,尤以厚壁部位明顯
- 內部氣泡或空洞,導致結構強度不足
- 短射與填充不完整
- 成品密度不足、尺寸不穩定
- 分子排列異常,影響機械強度與壽命
- 毛邊與閘口泛白
- 模具難以脫模或黏模現象
- 模內應力累積,導致翹曲或裂痕
- 設備負載過重,影響鎖模壽命與能耗
延伸閱讀:射出成型缺陷:原因及解決方案
為克服不同模穴厚度與流動長度對壓力需求的差異,許多現代成型製程採用多段保壓策略,此方法可分階段降低壓力與速度,使成型過程更平穩、缺陷風險更低。
- 第一段:高壓低速,穩定填滿關鍵區域
- 第二段:中壓低速,補償主體收縮
- 第三段:低壓維持,減少泵浦負載與能耗
- 控制內應力分布,降低變形與翹曲
- 穩定複雜產品的尺寸與重量
- 保護模內嵌件,避免位移損壞
- 節能降耗,提高設備壽命
隨著智慧製造趨勢興起,保壓控制已由傳統的經驗法則,邁向數據驅動的動態優化。
透過在模穴或流道內部安裝壓力感測器,能即時追蹤壓力變化範圍(100 ~ 3000 bar),並將數據回傳至射出機控制介面,有效掌握閘口封固點與每次成型波動。
透過導入PLC控制系統與機器學習演算法,系統可根據產品重量、壓力曲線與歷史紀錄,自動修正保壓參數,大幅提升保壓設定的穩定性與生產品質一致性。
射出成型的成功並非僅仰賴高速充填與高壓驅動,而是來自於每一階段精準穩定的控制。其中,保壓階段的參數設計與監控技術,正是決定產品一致性與製程效率的關鍵,唯有掌握正確的保壓壓力與時間設定原則,並搭配多段保壓策略與即時數據回饋技術,才能真正實現高品質、低缺陷的射出量產。
- 集團名稱: 華嶸集團
- 品牌: 華嶸、煜達、南嶸
- 服務項目: 射出成型機、立式射出機、成型設備取出裝置
- 服務電話: (06)7956777
- 集團總部: 台南市西港區慶安里中州21之6號
- 官方網站: https://www.huarong.com.tw/